Applying a Level 9 Proximity Detection System (PDS) to a mining operation is as much about changes in behaviour as it is about technical solutions, according to Pieter Wolfaardt from Apex, Booyco Electronics’ training partner of choice.
“An operational readiness assessment process conducted up front highlights all potential impacts on operations and pedestrian safety, giving the mine the opportunity to achieve seamless Level 9 integration with both the PDS and yellow fleet OEMs,” he says.
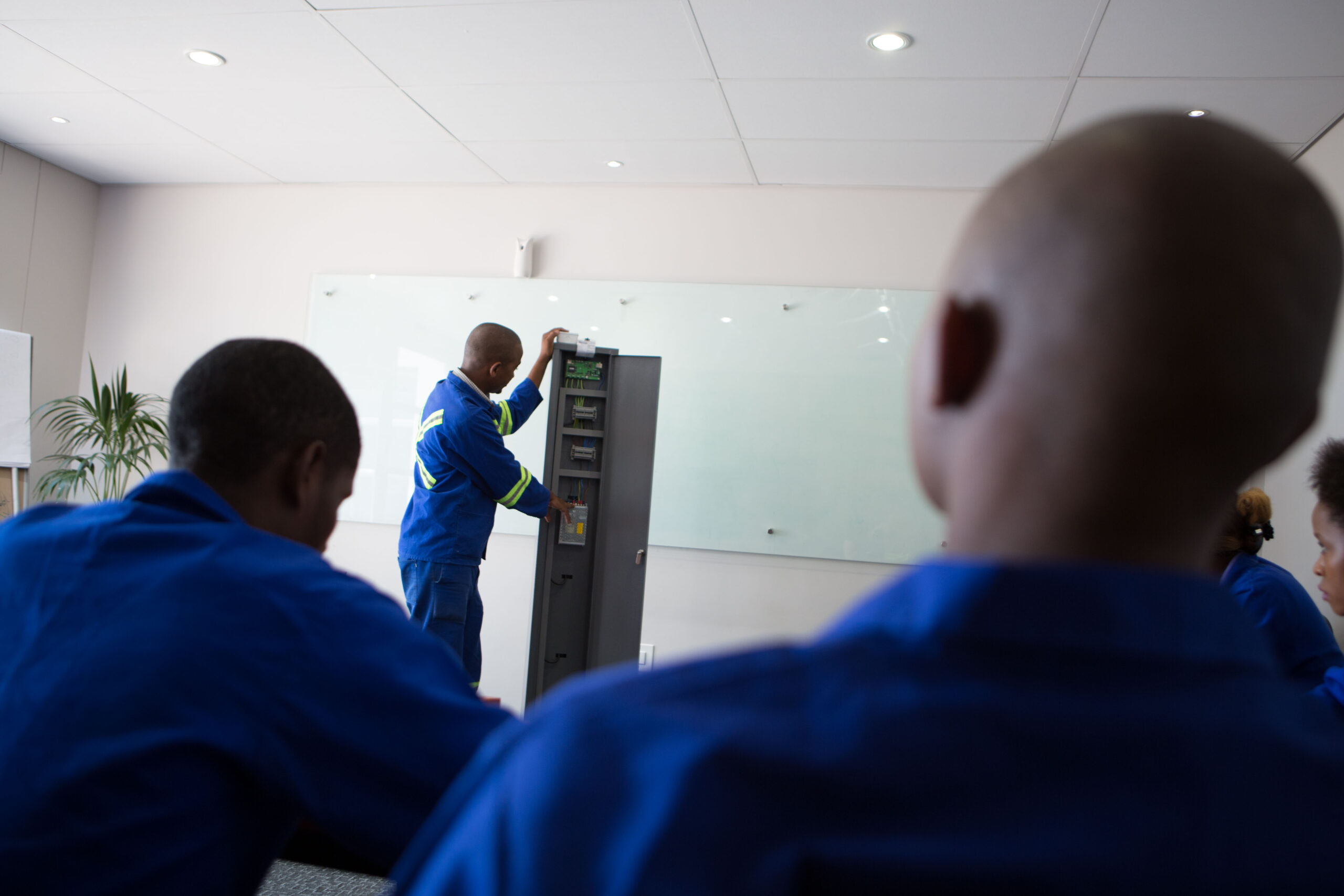
It is over two years since the South African Department of Minerals and Energy’s Level 9 intervention made it law to install PDS on all trackless mobile machines (TMMs). This is the latest step in the country’s journey as a global pioneer in this field. The advanced pace of regulation has also spawned a vibrant local economy of PDS developers and suppliers, in which Booyco Electronics has been a prominent player since 2006.
Wolfaardt highlights that there is well-proven Level 9 PDS technology available to mines, and it has been shown to significantly mitigate safety risk. However, the best results require more than technical installation; they require a systematic process of change management by all involved.
“Integrating a Level 9 PDS into a mining operation is not merely a technical upgrade; it fundamentally alters the way mines operate,” he explains. “Change management is the bridge that closes the disconnect between technology and people.”
He notes that the change process impacts safety culture, production and operator behaviour. Without structured change management, resistance to new protocols can undermine the system’s effectiveness.
“In our experience, a lack of change management often leads to a mine experiencing undue production stoppages, miscommunication and frustration among operators and managers,” he says.
By fostering better understanding and acceptance, change management ensures that safety improvements translate into long term shifts in behaviour – going beyond basic compliance to support a stronger culture of safety.
He explains that Apex, as the training service provider of choice to Booyco Electronics, addresses these challenges by ensuring that all stakeholders are involved and committed to the process. A vital starting point is a mine steering committee, ideally chaired by the general manager, to ensure alignment across departments from procurement and human resources to engineering and production. Apex then assumes its role as the Level 9 PDS change management facilitator and trainer on this committee.
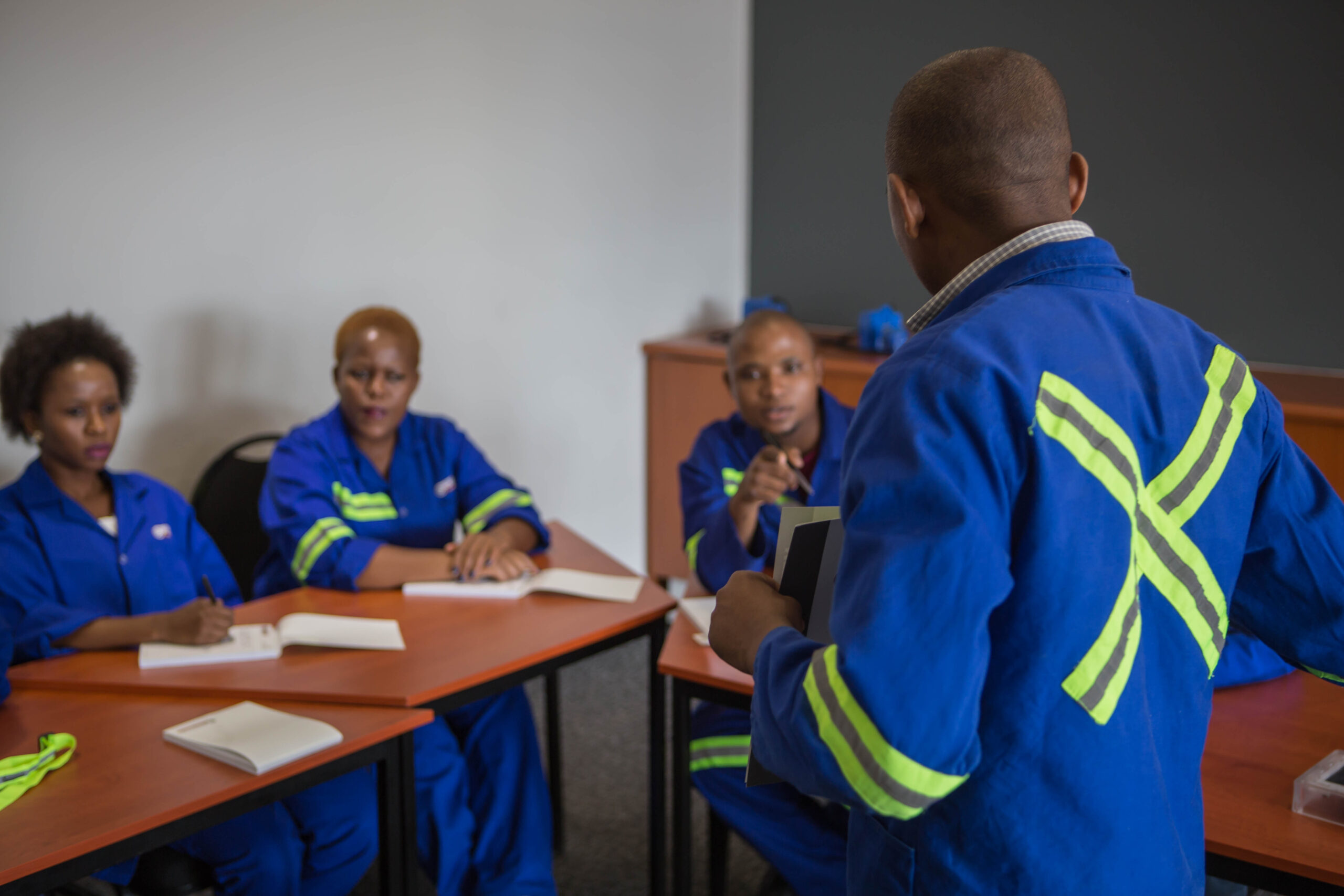
“Leadership commitment is the driving force behind successful Level 9 PDS adoption so when a general manager champions the change, it signals to employees that safety is a core priority,” he says. “At the same time, every department must buy into the process and recognise their role.”
A key aspect of the change management process focuses on the mine’s traffic management plan, part of the baseline risk assessment prescribed by the Machinery and Occupational Safety Act. This plan will identify all the vehicles and zones of significant risk on the mine, and starts with a traffic analysis.
“Developing a sound traffic management plan will ensure that the mine understands their current traffic situation: Which vehicles are in the TMM fleet? Where do they travel? How often, and at what speeds?” he explains. “The plan must also analyse aspects such as road conditions, illumination levels and ventilation – as well as the critical issue of interaction between machines, and between machines and pedestrians.”
It is important to identify pre-emptive traffic management adjustments that will minimise any disruptions and ensure that mining operations continue efficiently. Structured training is conducted with operators and other stakeholders, to understand the mine’s new operating dynamics.
“Training is a cornerstone of effective Level 9 PDS implementation, and needs to be based on the gaps that we identify in the system,” he says. “It focuses on people change management, and educates personnel on new protocols. This often goes beyond classroom training and should be tailored to operational needs.”
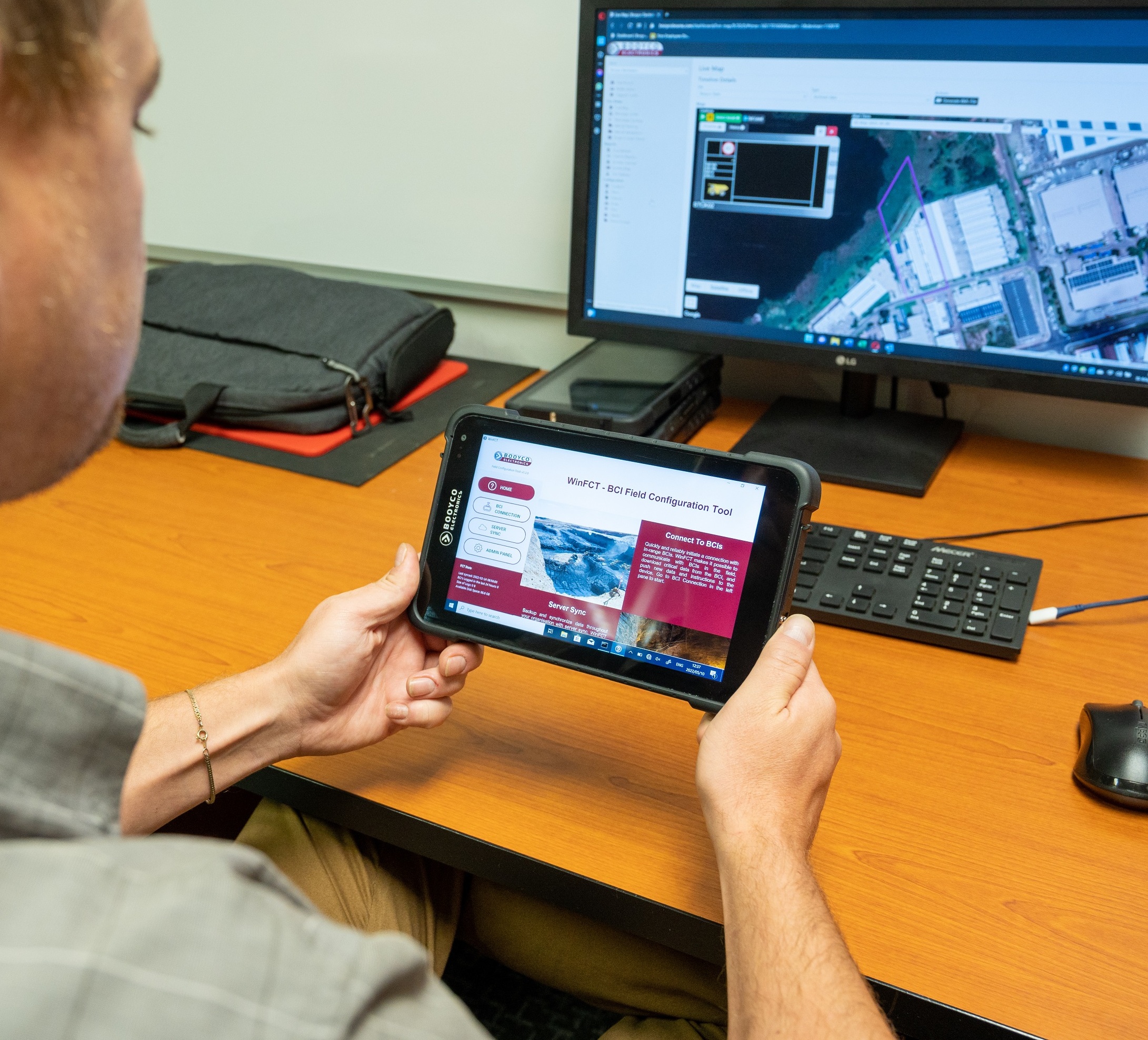
Effective communication strategies, such as regular briefings and transparent discussions about challenges, help to build trust and buy-in from employees. Engaging workers in safety committees and seeking their input on system refinements also promotes ownership of the change.