Following an extensive testing regime, Athos Crushing & Screening is officially launching a fully electric range of mobile crushers and screens called Powertrack, built by SRHeavy (SRH). Dubbed the Powertrack, the range initially comprises a mobile jaw crusher, a mobile cone crusher, a mobile triple-deck screen and a mobile scalping screen.
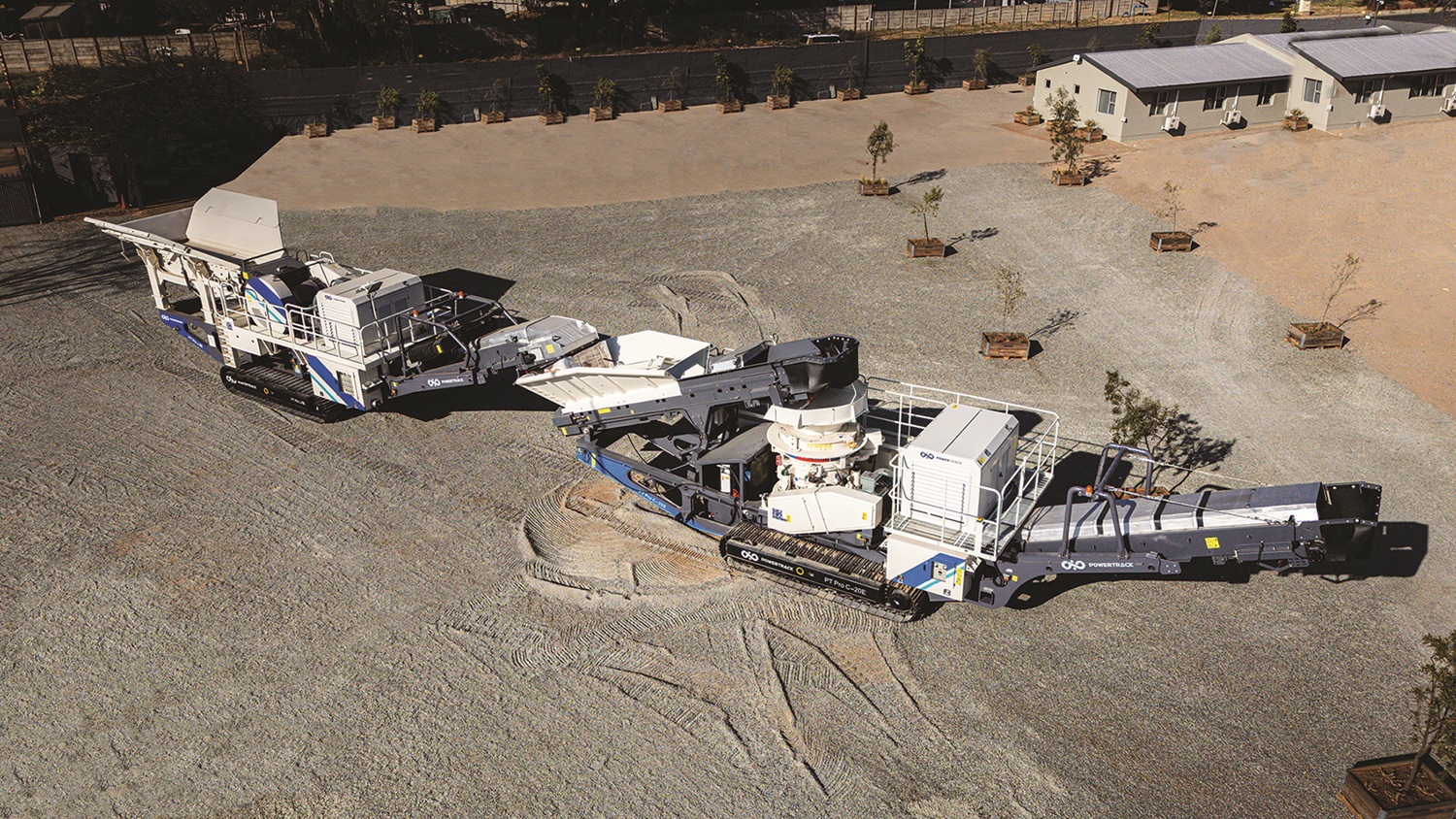
Athos Crushing & Screening, sister company to Pilot Crushtec International, was established some five years ago with the mandate to provide mobile and static crushing and screening solutions, focusing on entry-level and mid-tier segments of the market. The overarching intent, explains Sales and Marketing Director Francois Marais, was to create a true “home of crushing and screening” with Pilot Crushtec concentrating on the premium end of the market.
In line with this strategy, Athos is debuting the e-Power Powertrack range in southern Africa. At a launch event held at the company’s Jet Park in July, the company introduced the Powertrack PT Pro J-11E jaw crusher, the Powertrack PT Pro C-20E cone crusher, the Powertrack PT Pro ST-08E mobile triple-deck screen and the Powertrack PT Pro SP-08E scalping screen to local customers. Target markets, says Marais, include contractors, quarries and certain mining applications, particularly sites where there is access to grid power or renewable energy sources.
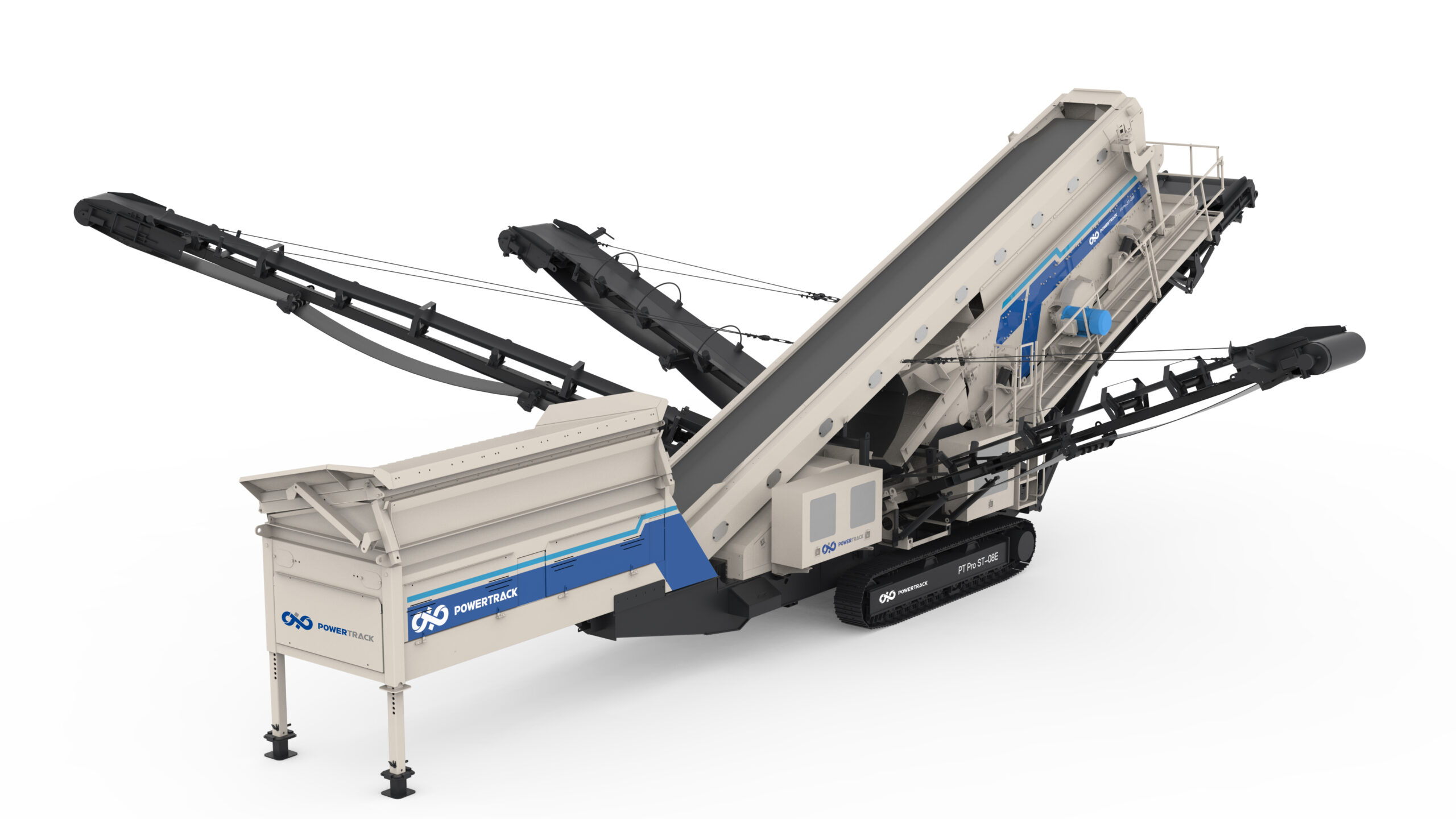
“Ideal for aggregates, mining and recycling, the Powertrack PT Pro J-11E is equipped with an SJC108 jaw crusher with a 1 060 x 700 mm feed opening,” explains Marais. “The machine can handle a top size up to 600 mm and typically runs with a closed side setting of about 70 mm. It has the capacity to process between 150 and 500 tonnes per hour (tph), application dependent.”
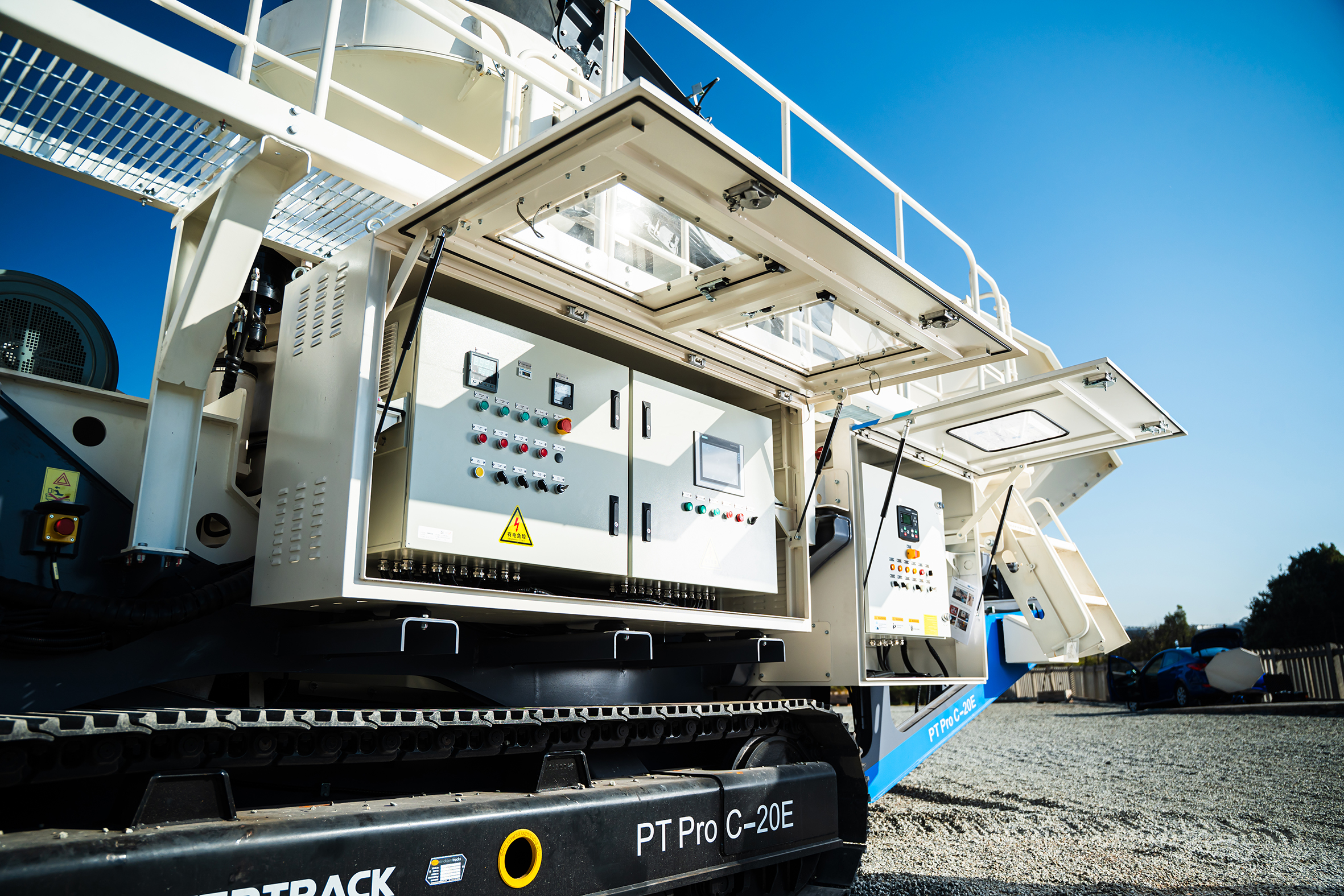
The Powertrack PT Pro C-20E, which features the SCH2000 cone crusher, is ideal for secondary and tertiary crushing. The machine has the capacity to produce between 150 and 250 tph, depending on application.
The Powertrack PT Pro ST-08E mobile triple-deck screen comes with a 5,4 m x 1 ,5 m screen box and a large 8,4 m² screening area. With its four product conveyors, it can be deployed in 250 tph production capacity requirements.
The Powertrack PT Pro SP-08E scalping screen, which comes with a 4,8 m x 1,5 m screen box, is ideal for pre-screening of feed with excessive fines such as topsoil, recycled waste and gravel, amongst others. The machine is designed to process capacities up to 500 tph.
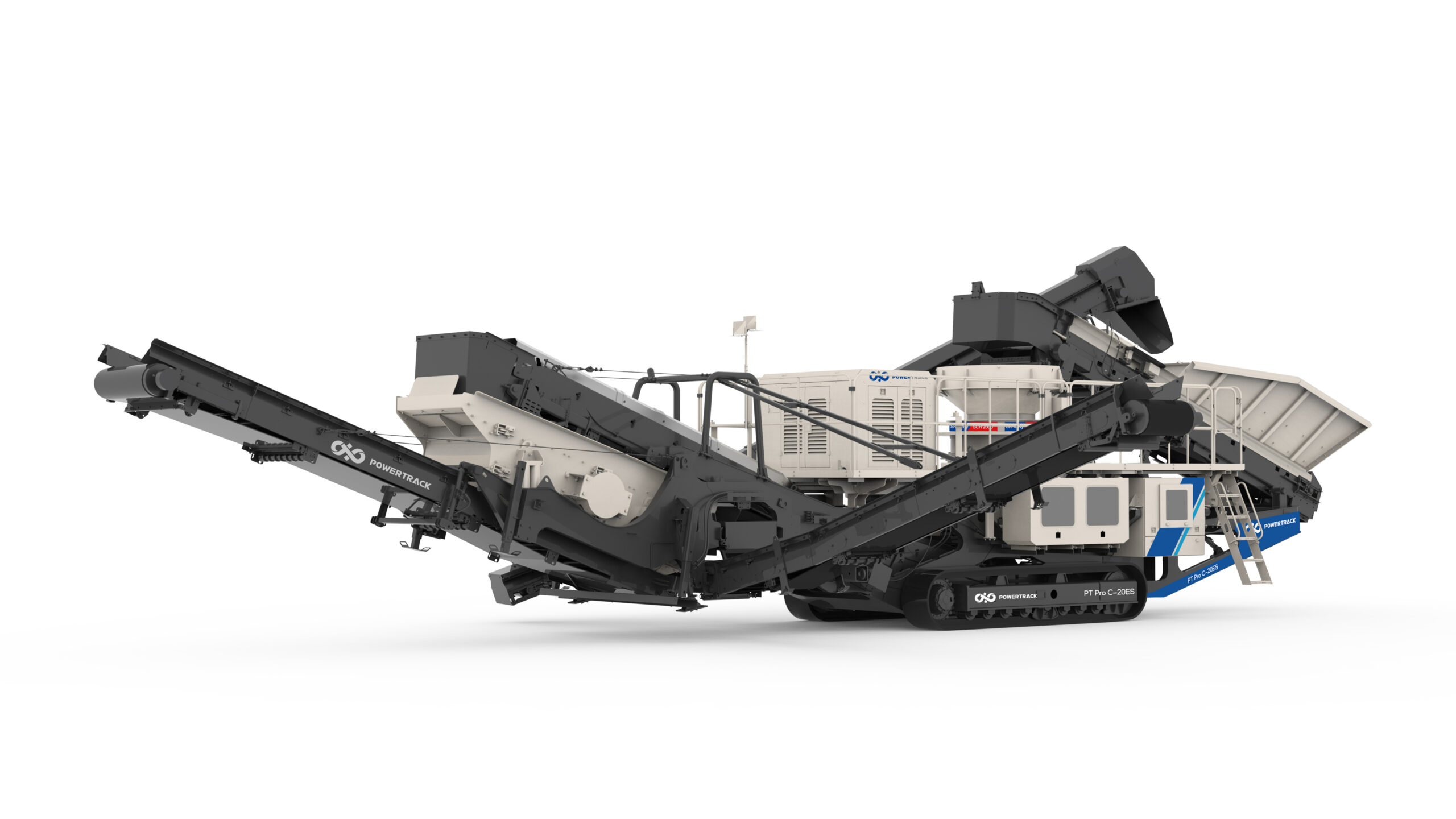
“A major factor behind the decision to go the fully electric route is that these machines come in at an extremely competitive price point,” says Marais. “Manufactured in China, inarguably the global leader in electromobility, the economies of scale for electric components such as electric drives provides for a notable cost advantage, making the e-Power Powertrack range an attractive crushing and screening solution for the local market, especially for cost sensitive, entry-level operations.”
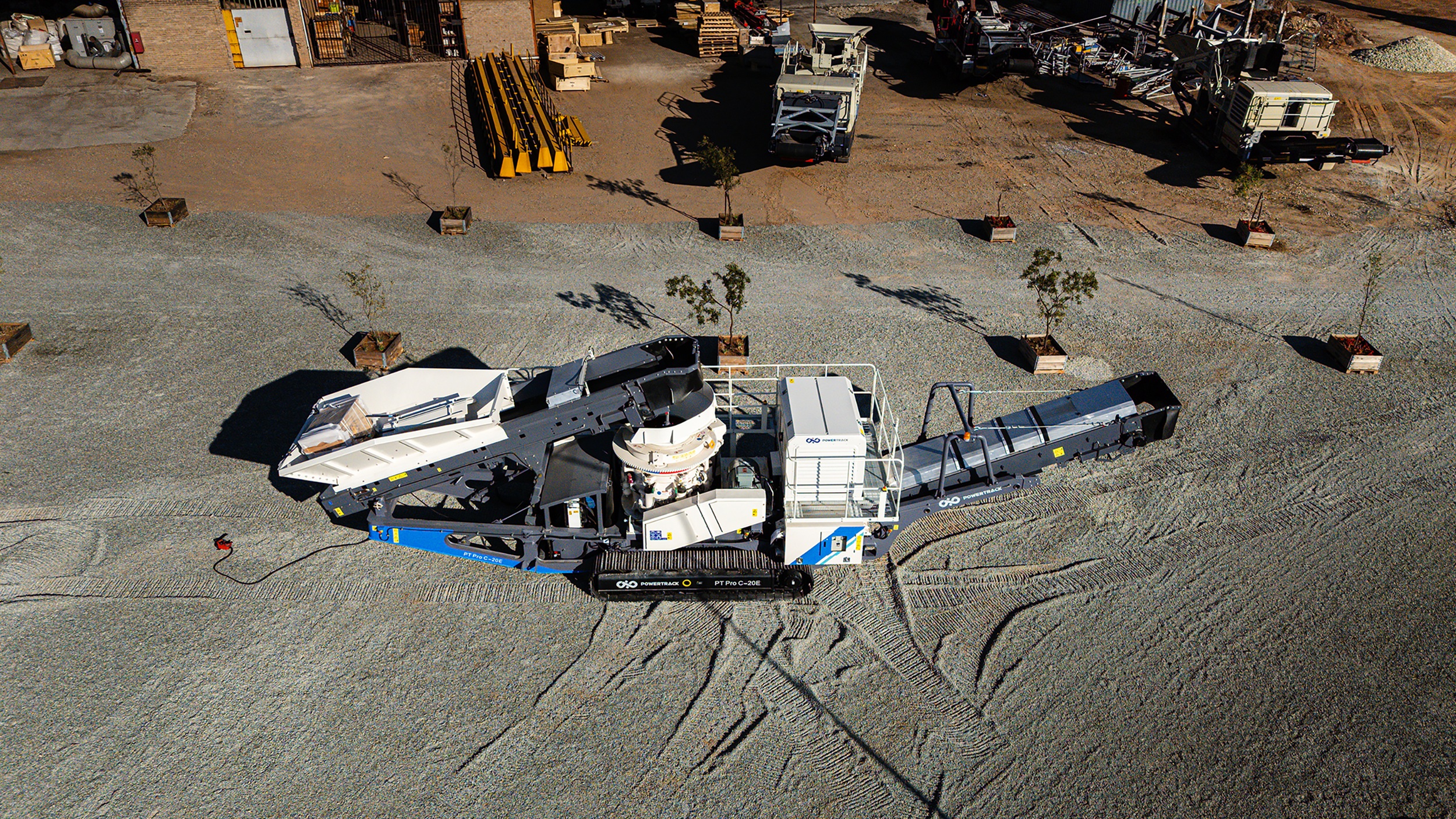
Another remarkable advantage of fully electric crushing and screening solutions is the lower cost of operation. These machines are primarily intended to be plugged into grid electricity. Electric drive systems are cost effective and more efficient than their conventional diesel hydraulic counterparts.
“In the absence of an electric plug-in, end-users can power the machine/s with a genset which, unlike in a dual-power setup, is completely separate from the mobile machine. This is a completely new concept in the local mobile crushing and screening market. One of the major benefits of keeping the generator away from where crushing takes place, is the elimination/reduction of dust ingression into the engine, which tends to be a major challenge for machines that come with an on-board genset,” concludes Marais.