At the end of the raiseboring – or reaming – stage for Shaft 2 of Ivanplats’ Platreef project in South Africa’s Limpopo province, an innovative solution was called for to promptly remove the reaming head and avoid costly standing time.
Fred Durand, Senior Project Manager at Murray & Roberts Cementation, explains that an acceleration of the build plan at Shaft 2 had seen construction underway on the shaft’s headgear in 2024 – before the completion of raiseboring.
“When a reaming head reaches the surface at the end of a raiseboring process, we normally use a mobile crane from surface to help us dismantle the machine and to load it onto trucks for removal from site,” says Durand. “With the acceleration of the mine’s plan for Shaft 2 readiness, however, the construction of the headgear had been brought forward – so it was no longer feasible to position a crane in that area to remove the raisebore machine.”
“The kibble winder was not installed yet, so we had to engineer our way out of this situation to reduce raisebore standing time costs,” he says.
The solution began with a visit from one of Murray & Roberts Cementation’s rigging specialists from the company’s Bentley Park training and technical facility near Carletonville. His concept was to make use of a reeve block – or pulley block – system and winch which could be secured with limited steel work at the bank elevation.
“We prepared a proposal which described how reeve blocks could be secured to the sinking sheave wheel floor steel work by means of slings and beam clamps,” Durand continues. “We would then use an eight tonne electrical winch, secured to the bank, to operate the reeve block system.”
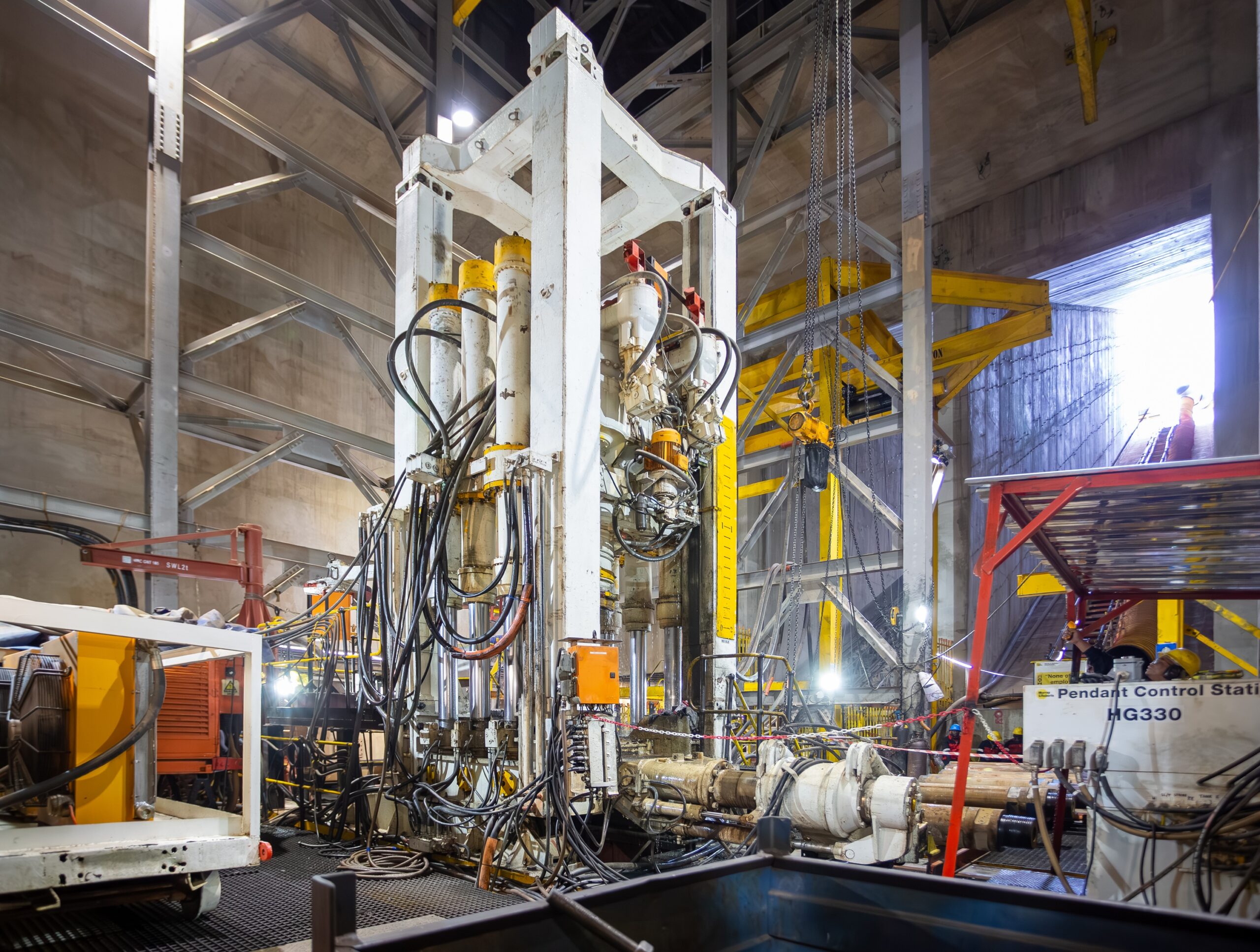
After the Murray & Roberts Cementation team were satisfied that the methodology would work, they conducted a rigorous risk assessment and prepared the necessary mitigation measures. The plan was then ready for the client’s consideration – leading to a green light to proceed. Personnel and equipment were soon mobilised, and the necessary medicals and inductions completed in preparation for the reamer coming to surface at the end of its 950 m journey from underground.
“Our solution worked perfectly, allowing us to strip the raisebore machine and hoist it to the bank area – to be placed onto the support bridge and moved out of the shaft headgear,” he says. “A mobile crane then lifted the machine onto the laydown area, ready for removal.”
Durand concludes that Murray & Roberts Cementation’s uncompromising approach to safe working practices ensured that this engineering solution was applied safely and efficiently within the tight timeframe. The company’s core safety values recently earned it the landmark achievement of 8 million fatality free shifts.