To increase energy efficiency and help reduce the climate footprint of the mining and quarrying sectors, Sandvik Rock Processing is leading the shift to electric mobile crushing and screening equipment. Essentially, by using less energy the industry can save money and operate in a more environmentally responsible way.
Mobile crushing and screening solutions remain prominent comminution solutions in both mining and infrastructure sectors. According to PC Kruger, Business Line Manager – Crushing at Sandvik Rock Processing, these solutions are renowned for their quick setup and deployment times, which makes them ideal for sudden spikes in demand. In addition, he says, as the industry continues to adopt in-pit crushing and conveying practices, mobiles can help do away with costly haulage trucks onsite, while reducing onsite traffic, dust and noise – increasing safety on site.
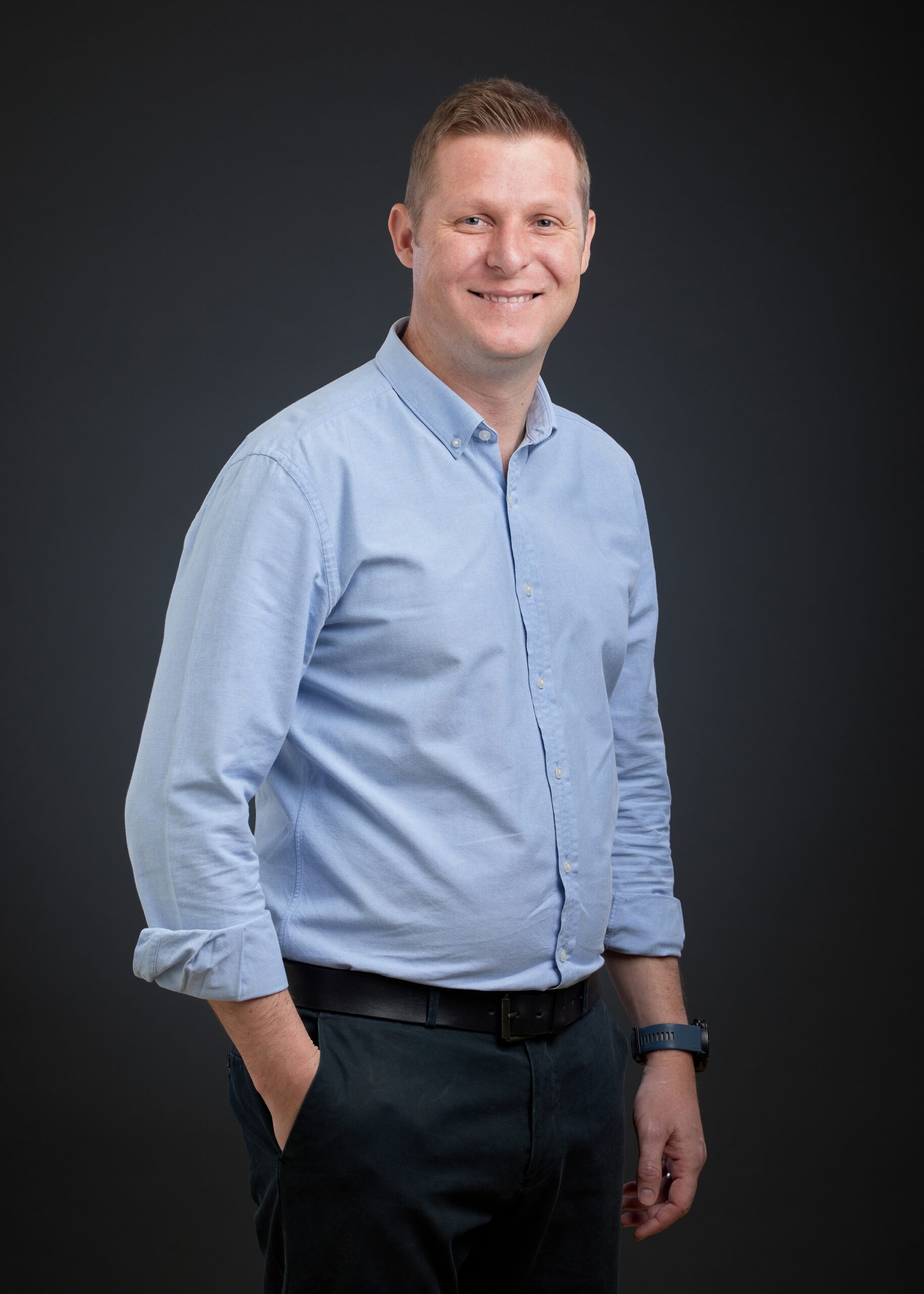
Another major attribute of mobile crushing solutions is their energy flexibility – the ability to be powered by electricity, diesel or both. To enhance energy efficiency and sustainability, the move to fully electric mobile crushers and screens has in recent years gathered pace. With its range of stationary and wheeled crushers and screens already 100% electrified, Sandvik Rock Processing has been one of the original equipment manufacturers at the forefront of the electric drive alternative.
“The most recent addition to our tracked electric range of crushers is the Sandvik UJ443E heavy duty jaw crusher. This machine is built on a new, ‘fully electric’ track platform. It features electric final drives and an on-board genset which can be operated more sustainably, either by an external electricity supply, hydrotreated vegetable oil (HVO) or diesel,” explains Kruger.
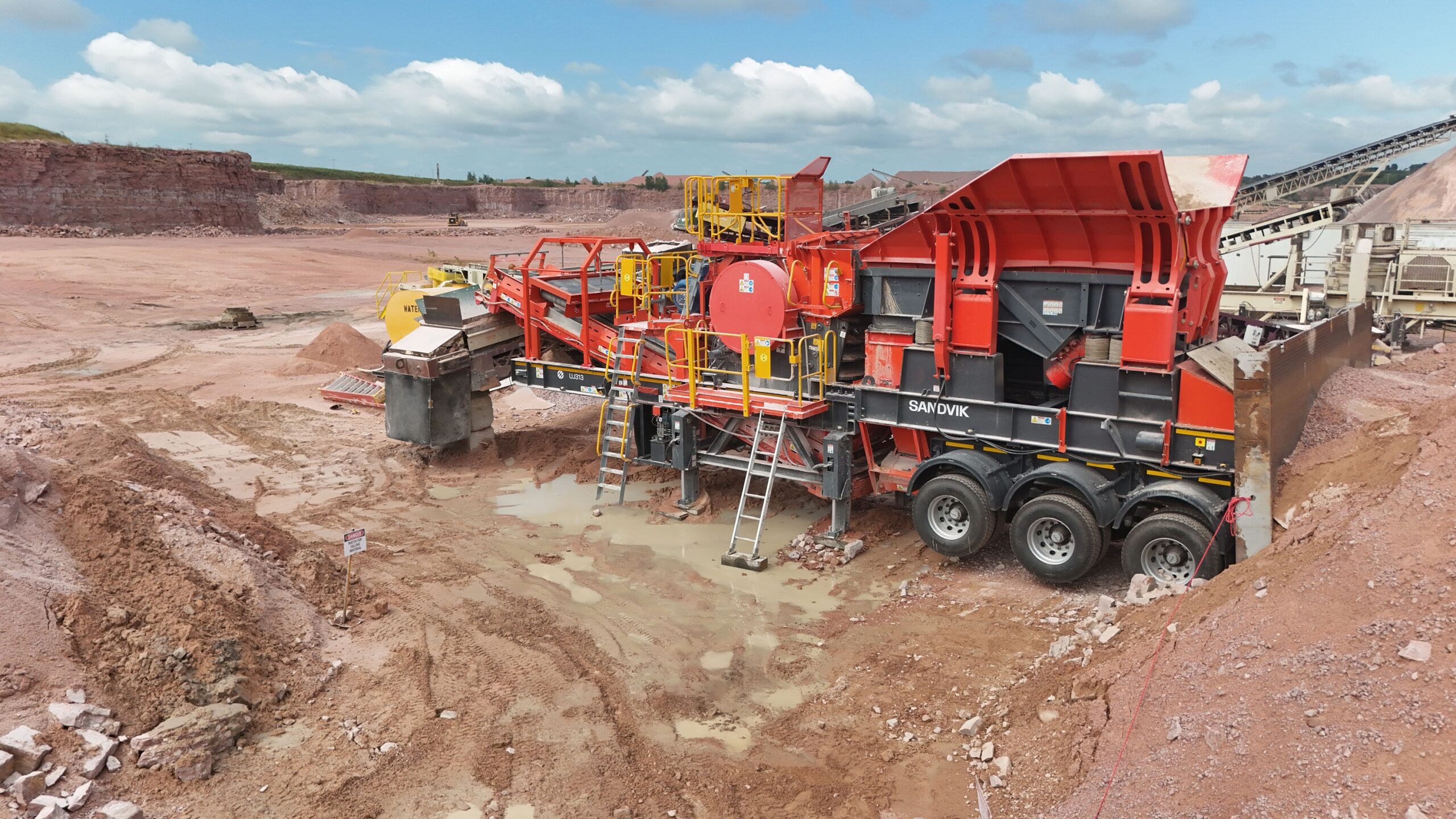
Operating the machine connected to the external electric source can bring several advantages including lowering running costs and noise levels, extending drivetrain service intervals and reducing time spent refuelling as well as reducing onsite emissions. Using fully electric track drives and final drives, the unit is said to decrease the use of hydraulic oil on the plant by up to 91%.
The Sandvik UJ443E features a 125 Amp downstream connection which allows customers to operate a downstream plant such as a screener or scalper, providing a decrease in fuel consumption of up to 20% compared to running separate units.
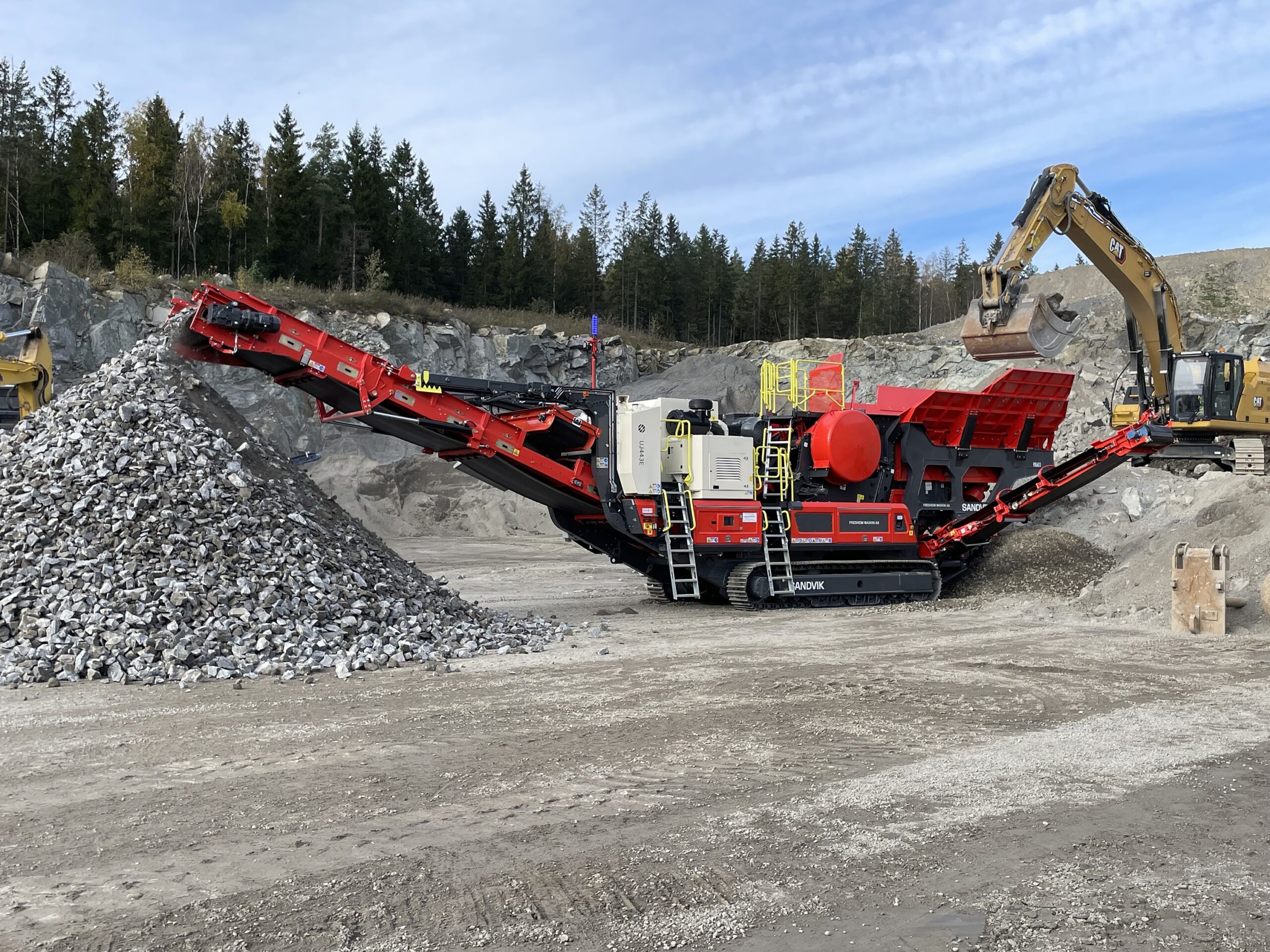
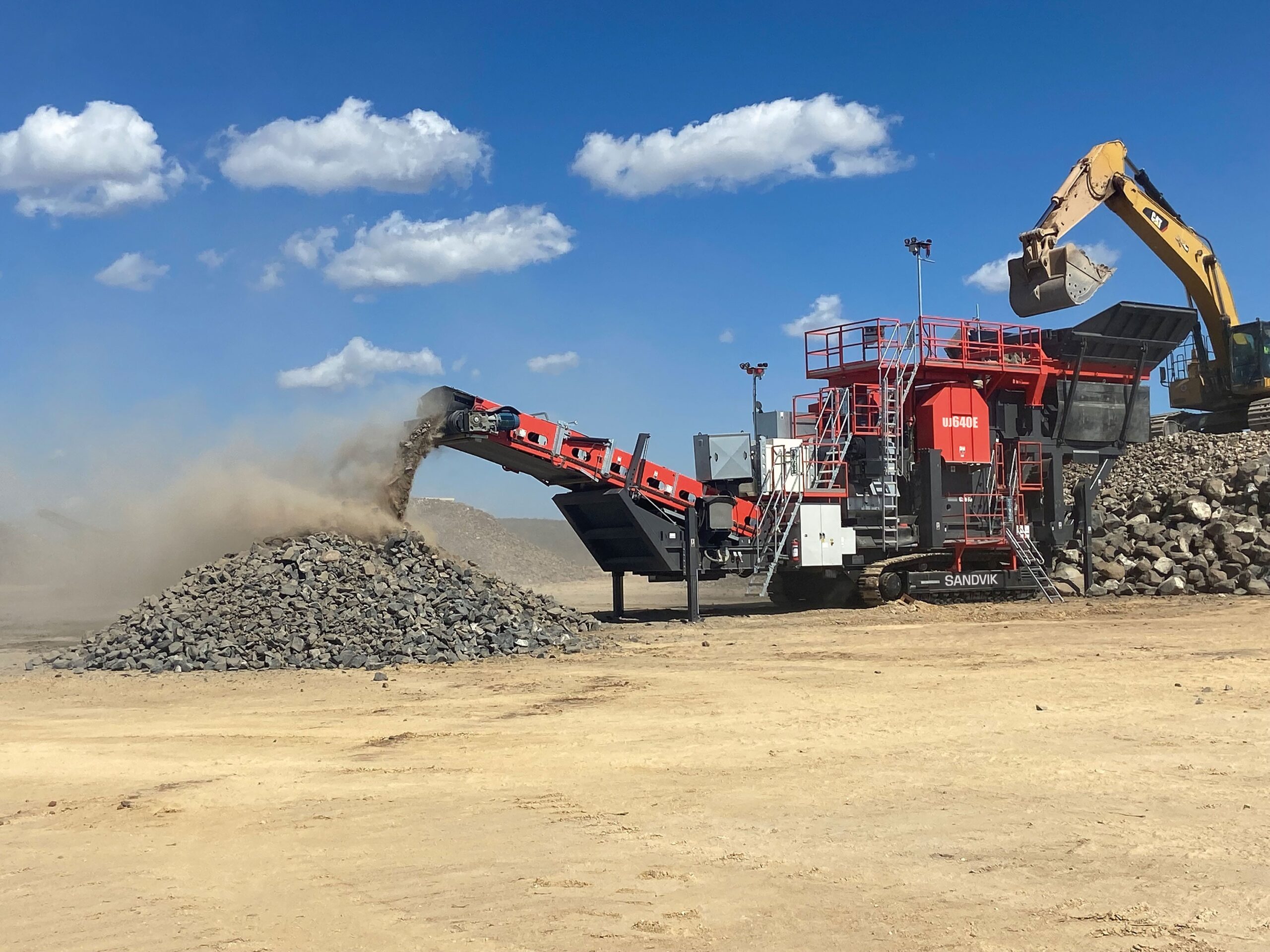
“In addition, our wheeled range of crushers has been made to meet the same high standards as its tracked counterparts, operating at maximum efficiency and designed for high-capacity production. Electrically powered, these units offer lower cost per tonne operation as well as lower emissions, minimising the environmental impact, which speaks directly to the industry’s sustainability drive,” Kruger concludes.