Mining trucks are monstrous machines that guzzle fuel at a scarcely believable rate.
Weighing 220 tonnes, they can get through 134 litres of diesel every hour.
Little wonder then that mining companies are focusing their attention on these vehicles as the first step to reducing their carbon footprint.
Anglo American, in collaboration with several partners, is retrofitting a mining haul truck with hydrogen power technology.
A first of its kind, the monster mining vehicle is being piloted in Limpopo, South Africa, at the firm’s Mogalakwena platinum mine.
Due to be launched in early 2022, the truck will be hybrid, with a hydrogen fuel cell providing roughly half of the power and a battery pack the other half.
Instead of having a tank of diesel that powers the motor, hydrogen enters the fuel cell and mixes with oxygen to create water in a chemical reaction catalysed by platinum, which generates the electricity needed to power the motors that drive the wheels.
It only emits water vapour and the company says it has the potential to reduce on-site diesel emissions by up to 80%.
By rolling out this technology across its global truck fleet, Anglo American says it will be “taking the equivalent of half a million diesel cars off the road”.
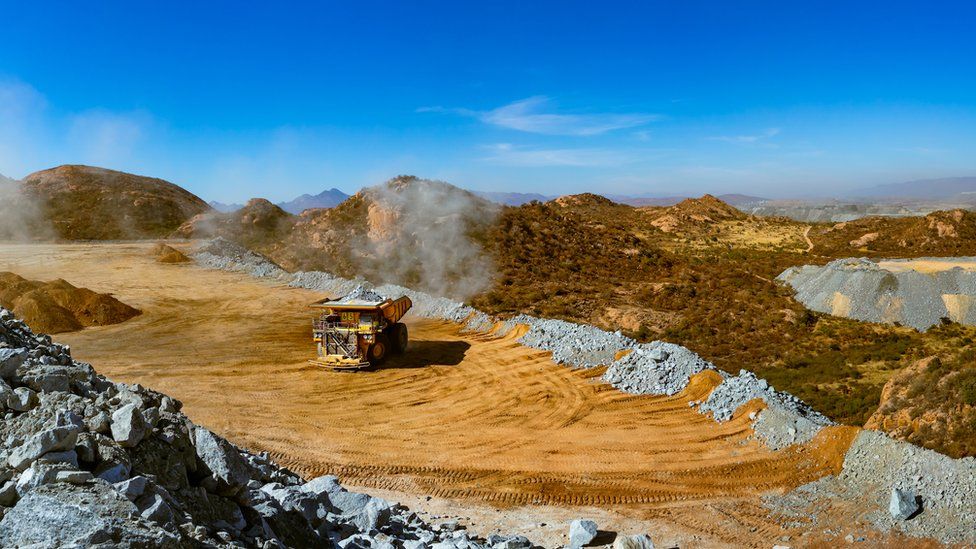
The trucks also harvest regenerative energy created when driving downhill and braking, which is stored in the battery and extends the range of the vehicle.
Anglo is developing the truck along with partners Engie, NPROXX, First Mode, Williams Advanced Engineering, Ballard, ABB, Nel and Plug Power.
However, reducing the carbon footprint of the mining industry is a formidable task.
The construction sector, which includes mining, accounted for 36% of global final energy use and 39% of energy-related CO2 emissions in 2017, according to Davide Sabbadin, senior policy officer for climate and circular economy at the European Environmental Bureau (EEB).
He says the sector will need to reduce its energy consumption by a third if it hopes to be compatible with the Paris Agreement.
Hydrogen-powered trucks are a good start but need closer inspection, says Diego Marin, associate policy officer for environmental justice at the EEB.
“While electric-powered vehicles, generally speaking, are less damaging to the environment than internal combustion engines on a life cycle analysis, this does not mean that they are green,” he says.
Mr Marin points out it all hinges on how the hydrogen is produced. Some hydrogen is created using fossil fuels, which of course means there are substantial emissions as a result.
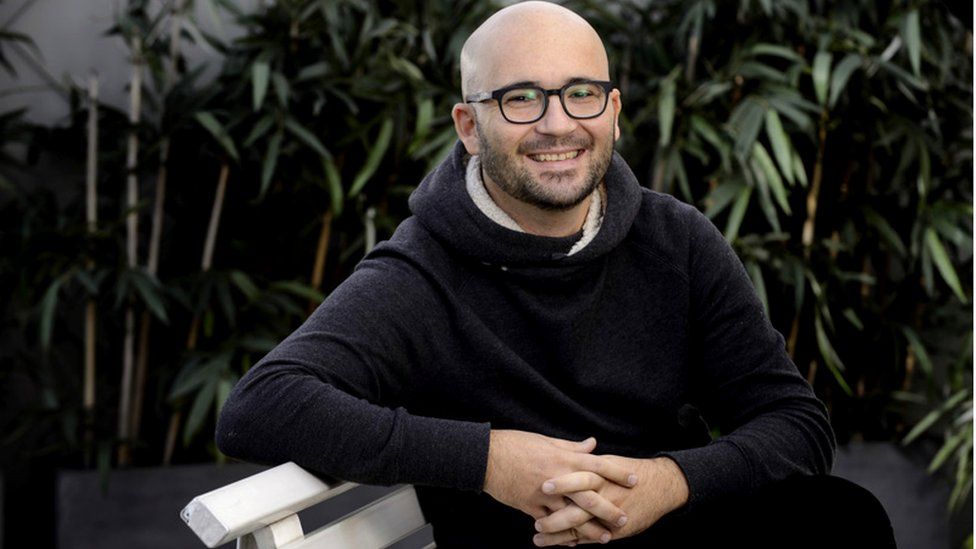
Anglo American says it is pulling out all the stops in an attempt to attain carbon neutrality by 2040.
Its hydrogen-powered hauler uses green hydrogen, which is made by splitting water atoms into oxygen and hydrogen, through electrolysis.
Even that is treated with caution by the EEB.
“We should refrain from presenting hydrogen as a technological solution to all problems… all forms of hydrogen come at an environmental cost – water use, impacts on nature,” says Mr Sabbadin.
The EEB also points out that hydrogen power has a shorter storage life than other renewables and is substantially more expensive to produce.
Whether it be investment for the mining industry’s green goals or hydrogen power as a broader power solution, the issue of cost is definitely a pertinent one in South Africa.
Jarrad Wright, an energy consultant and principal engineer for the Council for Scientific and Industrial Research (CSIR) explains.
“Hydrogen for power production is still quite expensive and unlikely to compete for some time.”
This is largely due to a lack of supporting infrastructure for the new forms of energy to be created, distributed or stored.
But, Mr Wright adds that it is possible to migrate to hydrogen in specific applications.
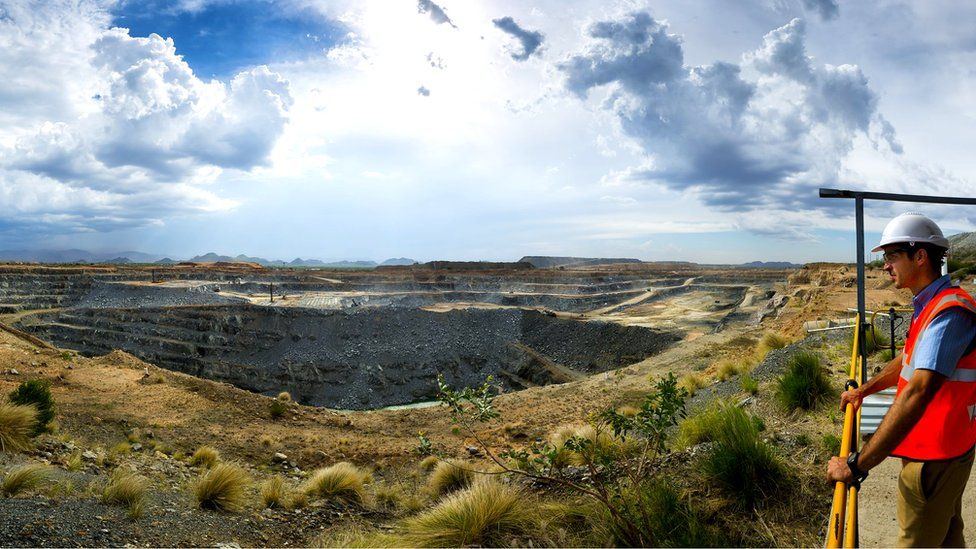
At the moment South Africa’s hydrogen power infrastructure is still sparse.
But the government and private partners are exploring ways to transform the country’s platinum belt into a “hydrogen valley”, with a focus on producing green hydrogen.
Anglo American is one of the private partners in this hydrogen infrastructure plan, which aims to create a regional renewable energy ecosystem.
The starting point for this ecosystem is due to be built at the Mogalakwena mine itself, through the construction of a hydrogen production and storage complex. It incorporates the largest electrolyser in Africa, a solar power field, and will generate approximately 140MW of green power.
Initially, it will be to support the 24-hour operation of the new truck, but once operational, the aim is for numerous complexes such as this one, to serve as local and regional hubs for the emerging hydrogen economy.
“The ecosystem would not only help us reduce our… emissions, but would also provide the foundation for green hydrogen production, facilitating the roll-out of hydrogen-powered haul trucks across South Africa,” Anglo says.