Technological advancements in the digital space are paving the way for a key trend in the management of transfer points: a transition from reactive to proactive maintenance.
Mark Baller, Managing Director of Weba Chute Systems, notes that chutes were traditionally replaced or repaired only after failure, resulting in unplanned downtime and higher costs. However, today’s leading mines are leveraging digital technologies to monitor equipment and processes in real time, enabling them to identify and resolve potential issues before they escalate.
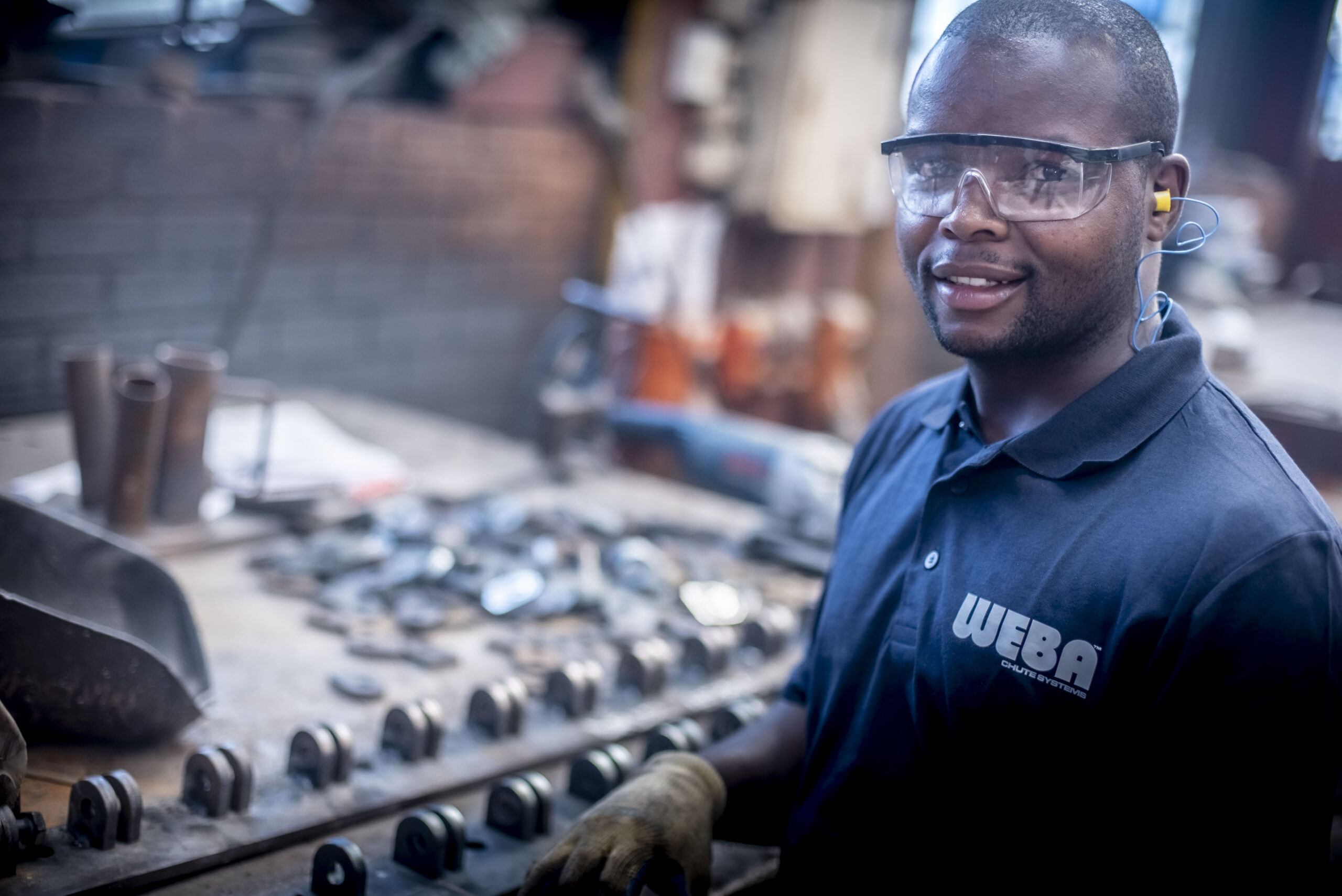
“This is certainly the direction in which transfer point technology is evolving,” says Baller. “Mining operations are increasingly leveraging data to prevent unplanned downtime and optimise equipment performance.”
He explains that the value of data begins with building a historical record of equipment condition and performance, enabling more accurate maintenance predictions. To support this, Weba Chute Systems has developed an inspection app that allows clients to monitor chute performance remotely. The app simplifies data collection and storage, enabling Weba to analyse trends and provide customers with informed maintenance recommendations.
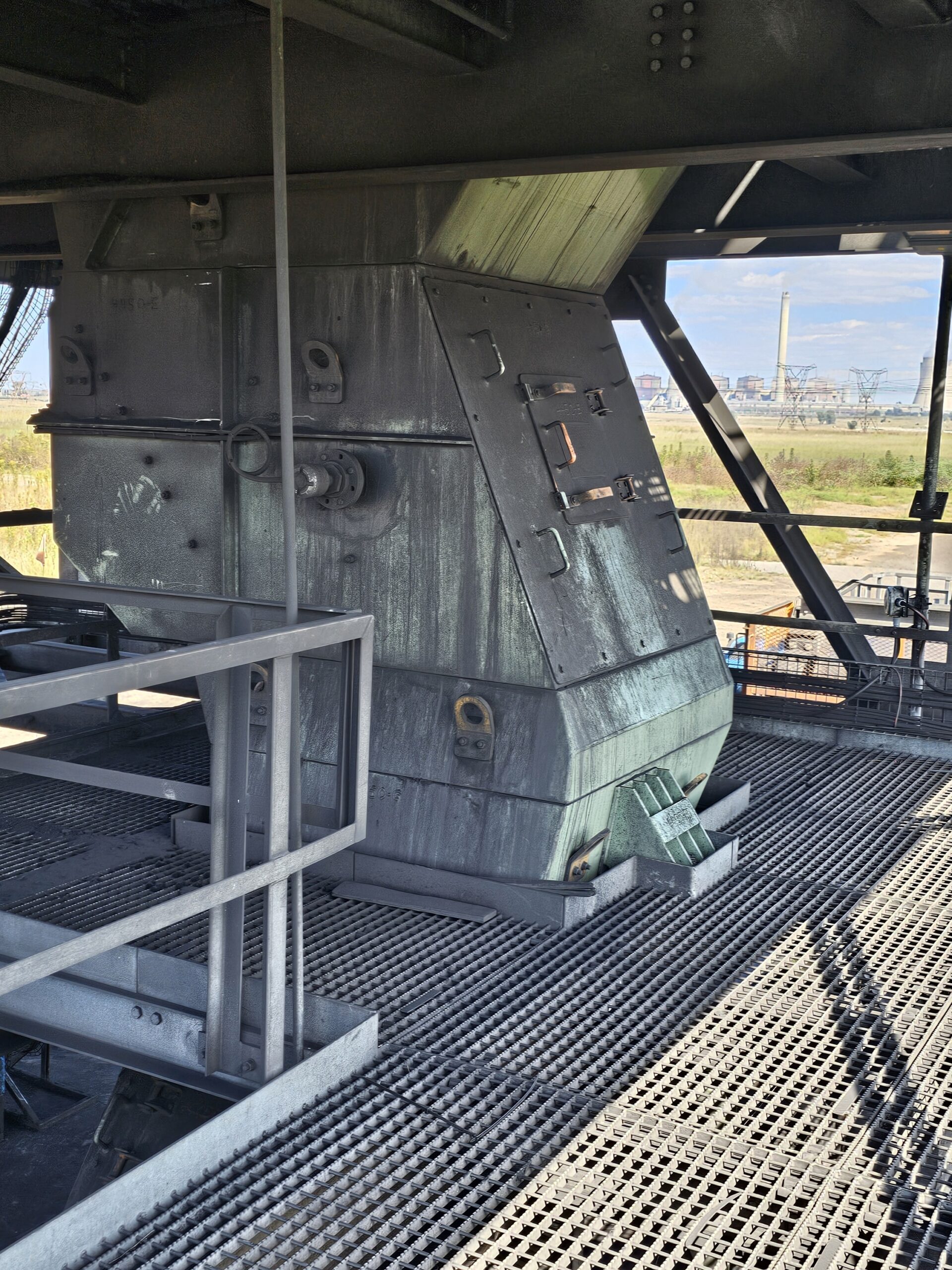
“With remote monitoring, we can identify trends and build a predictive maintenance model, allowing customers to schedule maintenance more efficiently,” Baller explains. “This level of transparency strengthens our partnership with clients and enhances the overall efficiency of their operations.”
He emphasises that an improved maintenance strategy not only increases operational uptime but also extends equipment lifespan. This reduces capital expenditure and minimises steel wastage while maximising the customer’s return on investment in the chute. Enhanced predictability also streamlines the supply chain, allowing both the OEM and the customer to anticipate spare parts requirements in advance.
Another key advancement for Weba Chute Systems is the move towards standardising chute components. While the company is renowned for its custom-built transfer chute solutions, it has been developing standardised components that can be used across multiple chute installations. This approach enhances efficiency, reduces lead times and streamlines maintenance.
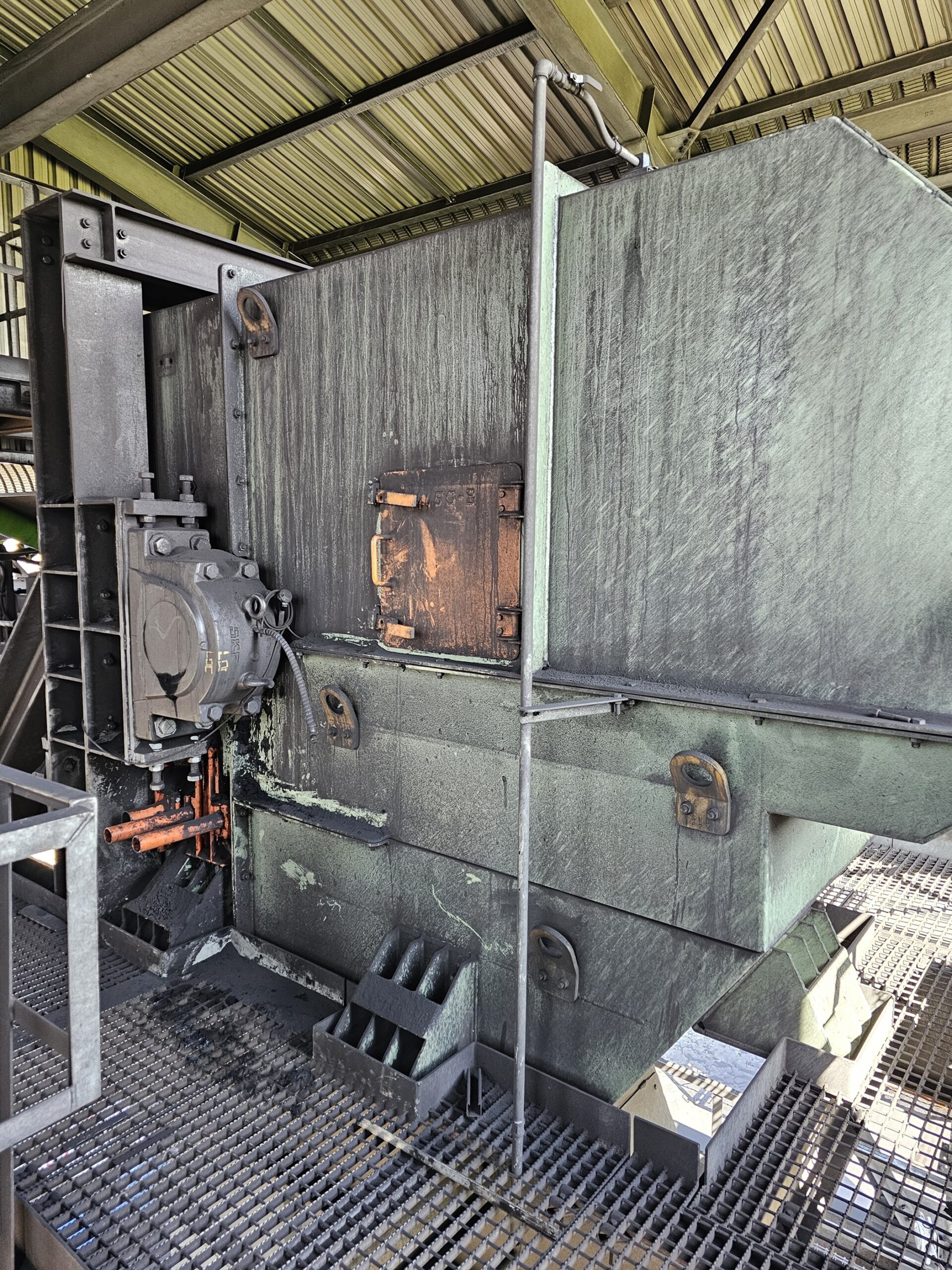
“Previously, every chute required custom components, forcing clients to keep a variety of different parts in stock,” Baller explains. “Now, we are shifting towards more standardised components, enabling clients to streamline their stockholding while still maintaining the flexibility to meet their maintenance requirements efficiently.”
This transition is especially advantageous for large mining operations with multiple chutes. By introducing component interchangeability, Weba Chute Systems is helping clients reduce operational costs while enhancing equipment longevity and overall efficiency.
Health and safety continue to be key considerations in chute selection, and Weba Chute Systems’ advanced designs optimise material flow while minimising turbulence, significantly reducing dust generation. Baller emphasises that a well-designed chute is often a more effective solution for dust control than relying on dust extraction systems.
The cost of installing and maintaining a dust extraction system can be significant and if the chute design itself generates excessive dust, the system may not be very effective,” says Baller. “Our chutes have demonstrated that a well-engineered design can eliminate the need for a separate dust extraction system, helping customers avoid unnecessary expenditure.”
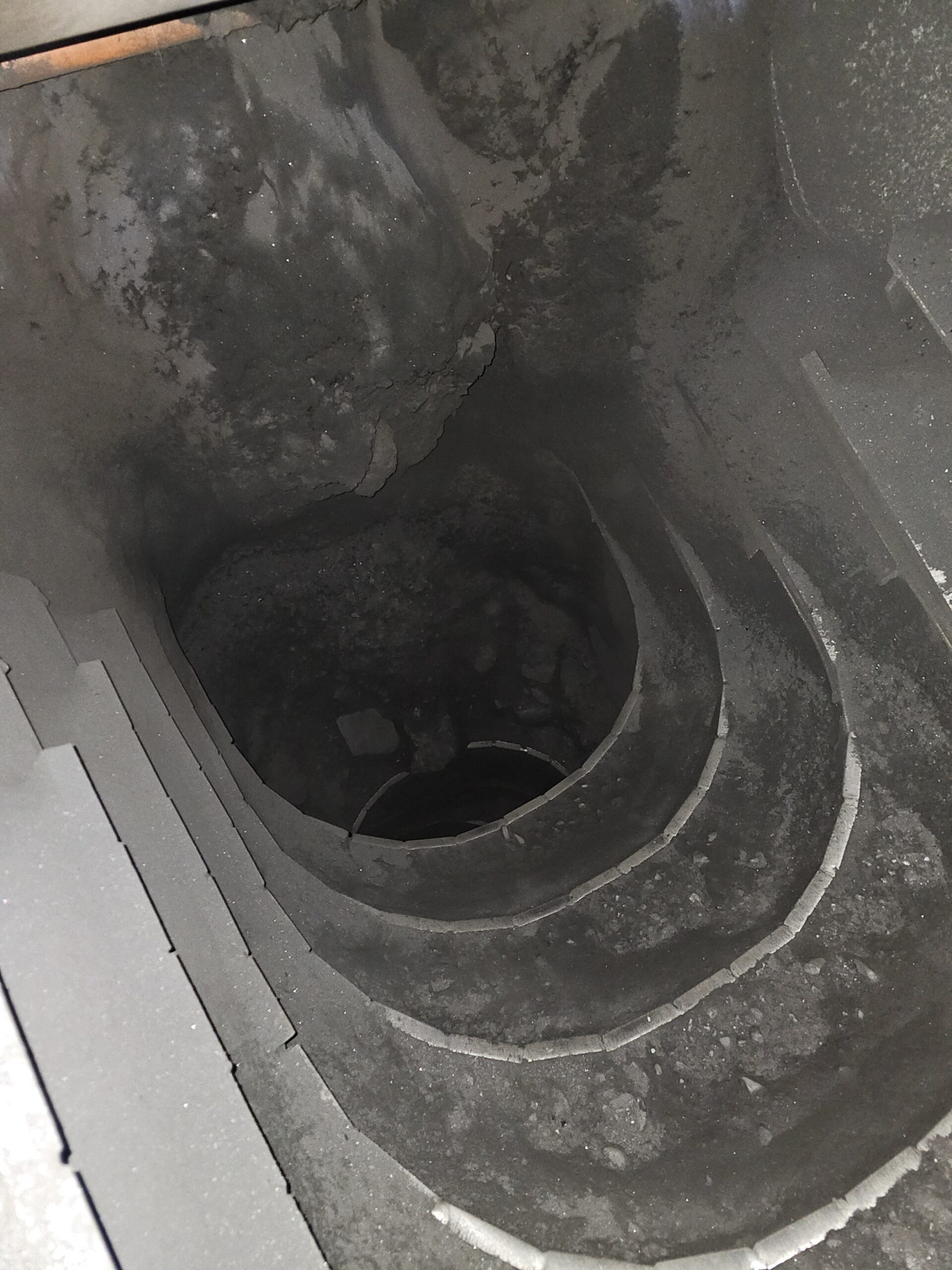
A prime example is a coal mine in the United States that was at risk of being shut down due to environmental concerns over excessive dust. After switching to Weba Chute Systems’ innovative technology, the results were remarkable.
“The customer was able to remove their dust extraction systems entirely because our chutes alone produced even less dust than their previous system did with extraction in place,” Baller explains.
The proven success of Weba Chute Systems’ designs has driven strong growth across sub-Saharan Africa, with an expanding footprint in the Middle East, Australia, Canada and the United States.
“We are particularly excited about opportunities in the Middle East and North Africa,” Baller says. “In markets like Australia and North America, our strategy focuses on engineering and design, while local partners manage fabrication. This approach allows us to leverage our expertise while ensuring efficient service to local industries.”