Sandvik Rock Processing is making it easier than ever for mining operations to cut costs and improve efficiency with its innovative X-change programme. This initiative allows mines to upgrade outdated spiderless and legacy hydrocone crushers with the next-generation Sandvik 800i series cone crushers – and the return on investment can be seen almost immediately.
According to PC Kruger, Business Line Manager – Crushing at Sandvik Rock Processing, the real value lies in how this programme helps operations reduce their total cost of ownership while optimising performance. “By taking advantage of the X-change programme customers can replace older technology with our high-performing Sandvik 800i range at a special price, while also gaining access to warranty support, ramp-up assistance and Sandvik’s advanced digital tools, all of which add up to significant operational savings.”
Kruger explains that customers upgrading through the X-change programme can expect up to 30% improved availability and up to 25% more final product delivered to downstream processes. This enhanced performance is due in large part to the Sandvik 800i’s state-of-the-art automation and robust mechanical design.
Equipped with the Sandvik ACS-c 5 automation system, the 800i crushers offer rapid liner calibration – completed in just five minutes – helping to reduce downtime and boost productivity. The automation system also includes role-based functionality, guided alarm responses for operators and full access to historical and real-time data for maintenance teams, empowering proactive planning and accurate performance monitoring.
On the mechanical side, the Sandvik 800i series is built for durability and efficiency. It features a direct-drive design that reduces energy loss, a strong unibody structure and top-down maintenance access that simplifies servicing. Other enhancements, such as Constant Liner Performance (CLP) chambers as well as a huge variety of chamber profiles to adapt to every unique application, double-sealed pinion shafts and non-welded bottom shell wear liners with plastic-free fasteners, all contribute to reduced maintenance requirements and longer wear life.
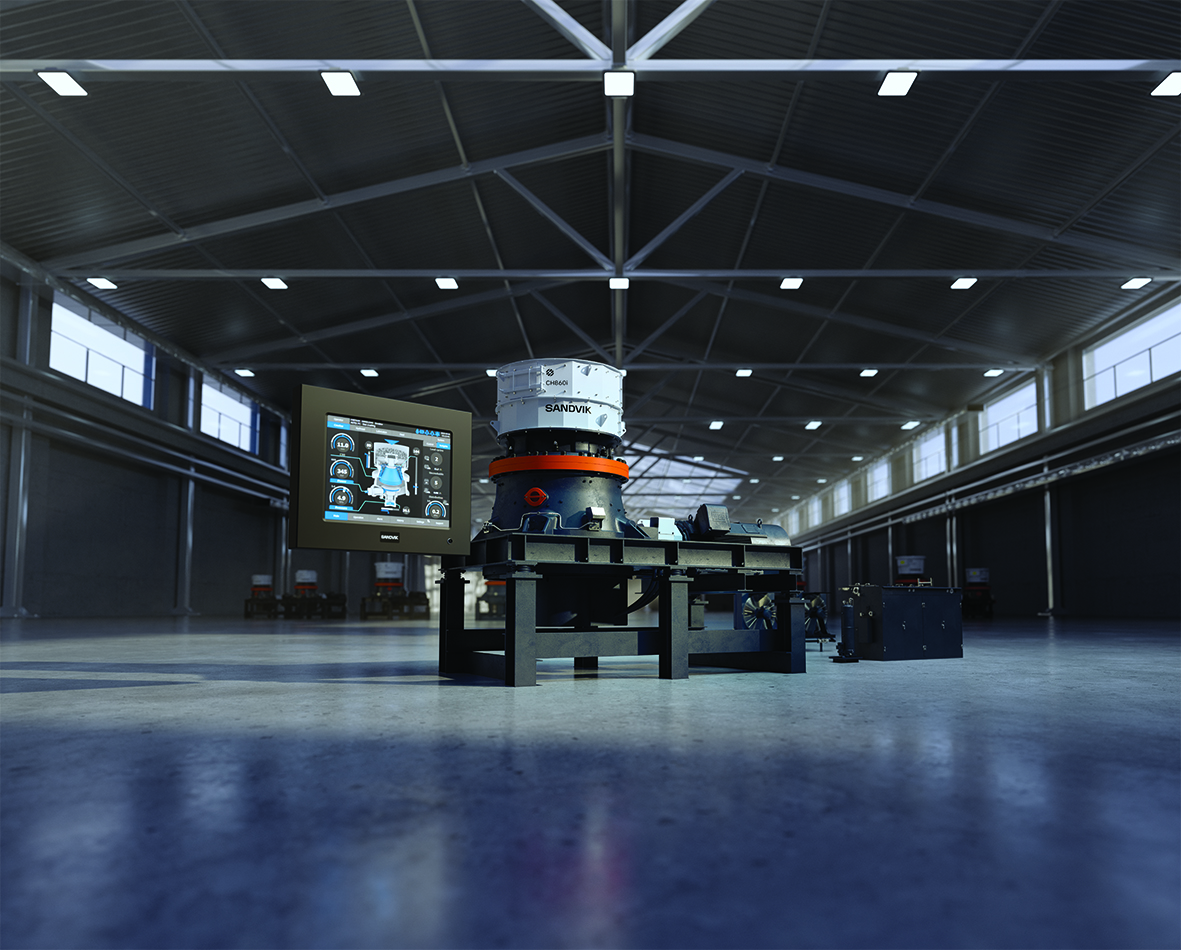
The Sandvik 800i range supports sustainable efficient operations in a wide variety of applications including three-stage crushing circuits, SAG/AG mill pebble crushing, heap leach operations, lump ore processing and integration with HPGR systems. These cone crushers are designed to deliver finer particle sizes, enhancing downstream performance and reducing energy consumption across the board.
Importantly, every Sandvik 800i crusher is fully compatible with SAM by Sandvik, the company’s cloud-based digital assistant. Through SAM, customers can monitor equipment in real time, receive alerts, track performance and order parts – streamlining operations and enhancing decision-making.
Kruger emphasises that the X-change programme is more than an upgrade and is a strategic opportunity for mines under pressure to increase efficiency, reduce energy consumption and extend asset life. With structured pricing, digital support and reliable aftermarket services built in, the programme provides a clear and cost effective pathway to modernising crushing circuits.
“Upgrading to the Sandvik 800i via our X-change programme provides a structured path to improve safety, increase availability and enhance productivity across crushing operations,” Kruger concludes.