FLS has completed a significant upgrade to its polyurethane manufacturing facility in Delmas, Mpumalanga, positioning the site as a key global hub for the production of its advanced NexGen wear -resistant material. This development forms part of a wider modernisation programme by FLS, aimed at strengthening supply chains, increasing manufacturing efficiency and enhancing sustainability across its global footprint.
Brad Shepherd, Director Service Line – Screen and Feeder Consumables at FLS, says the investment at Delmas aligns with the company’s global strategy to standardise and optimise production processes.
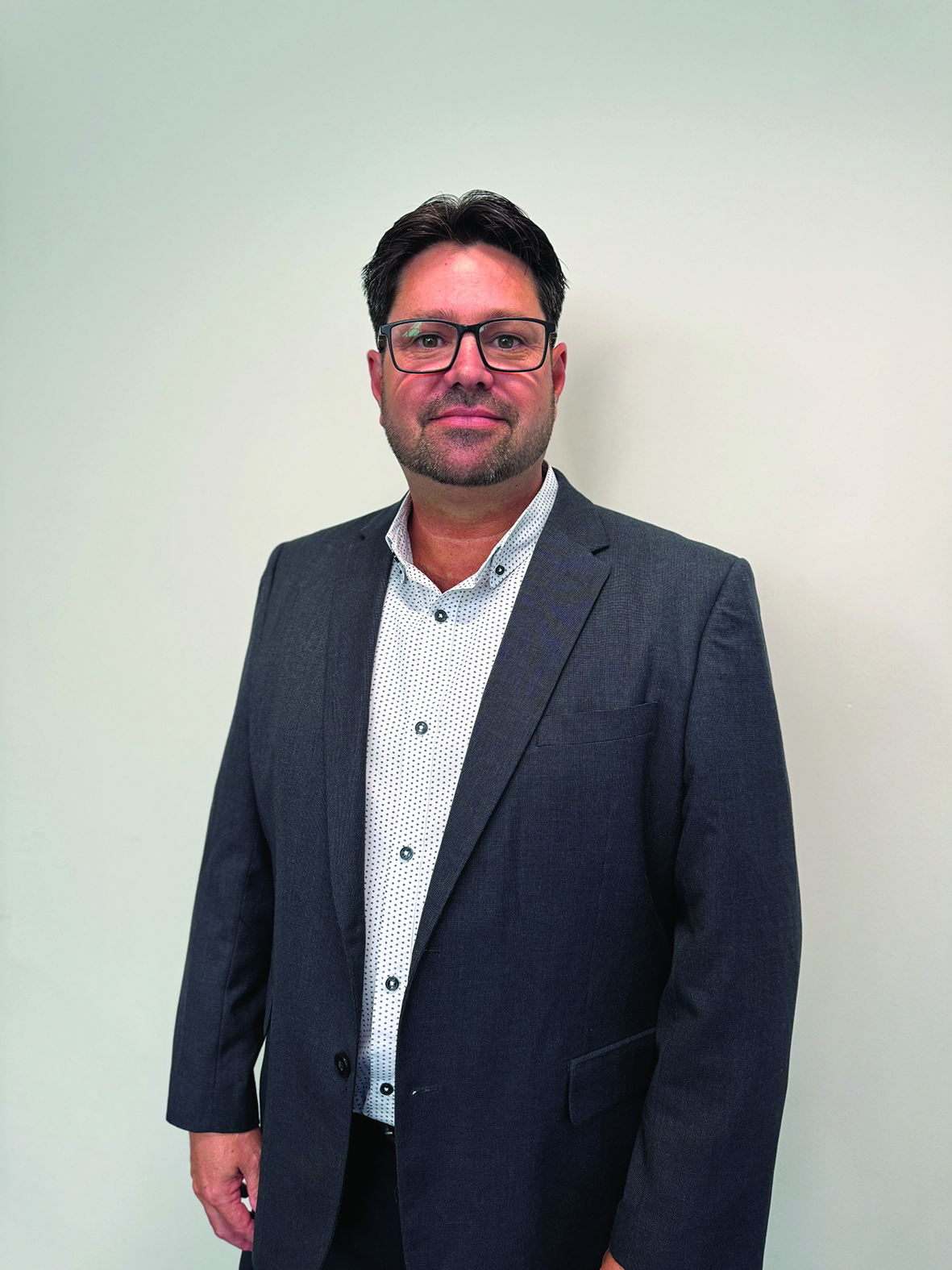
“This is a milestone for us,” says Shepherd. “We are integrating cutting edge technology and modern manufacturing methodologies across all our polyurethane plants, and Delmas is leading the way. The upgrade enables us to respond more quickly and reliably to customer needs across Africa, the Middle East and Europe.”
The centrepiece of the upgrade is the introduction of purpose-built infrastructure to produce NexGen screen media – a polyurethane material developed by FLS to deliver extended wear life, reduced maintenance and improved operational efficiency. In on-site trials, screen panels made from NexGen have demonstrated up to three times the wear life of conventional rubber and polyurethane products, making it a gamechanger for industries that rely on high performance screening solutions.
Warren Walker, Head of Global Manufacturing – Polyurethane Operations at FLS, explains that Delmas is the first of the company’s five global polyurethane plants to complete this transition. “We have installed new, latest generation polyurethane machines, precision tooling and dedicated preheating ovens for inserts,” he says. “This allows us to significantly increase our output while ensuring consistent quality.”
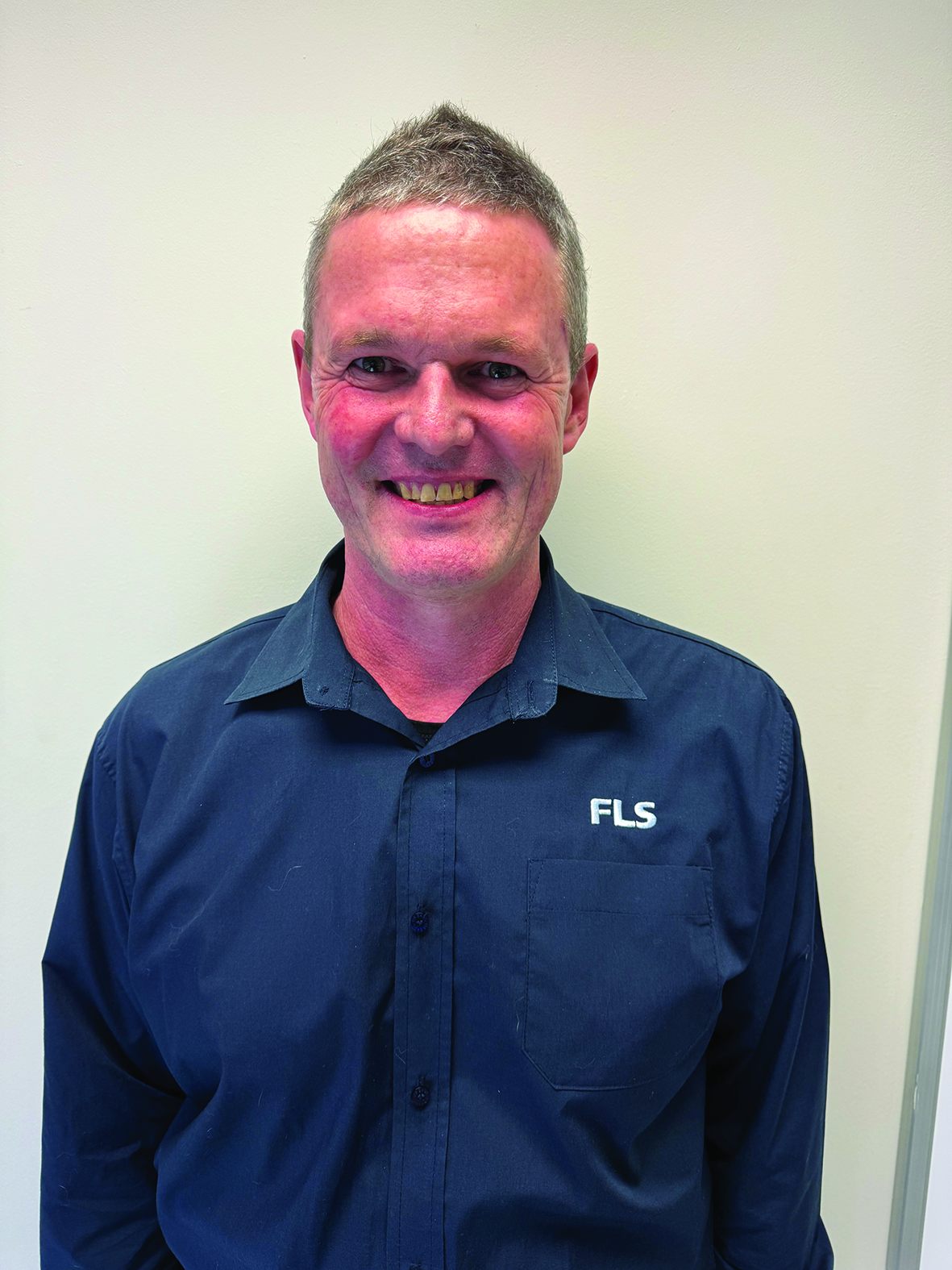
The facility now includes two trommel screen media stations and three screen media stations, each tailored to produce NexGen products. One of the standout technologies introduced is a programmable auto-calibrating polyurethane machine capable of adjusting material hardness to suit specific applications.
“The flexibility to produce varying hardness levels is critical,” Walker notes. “It means we can tailor our screen media precisely to the customer’s application, ensuring optimum performance and longevity.”
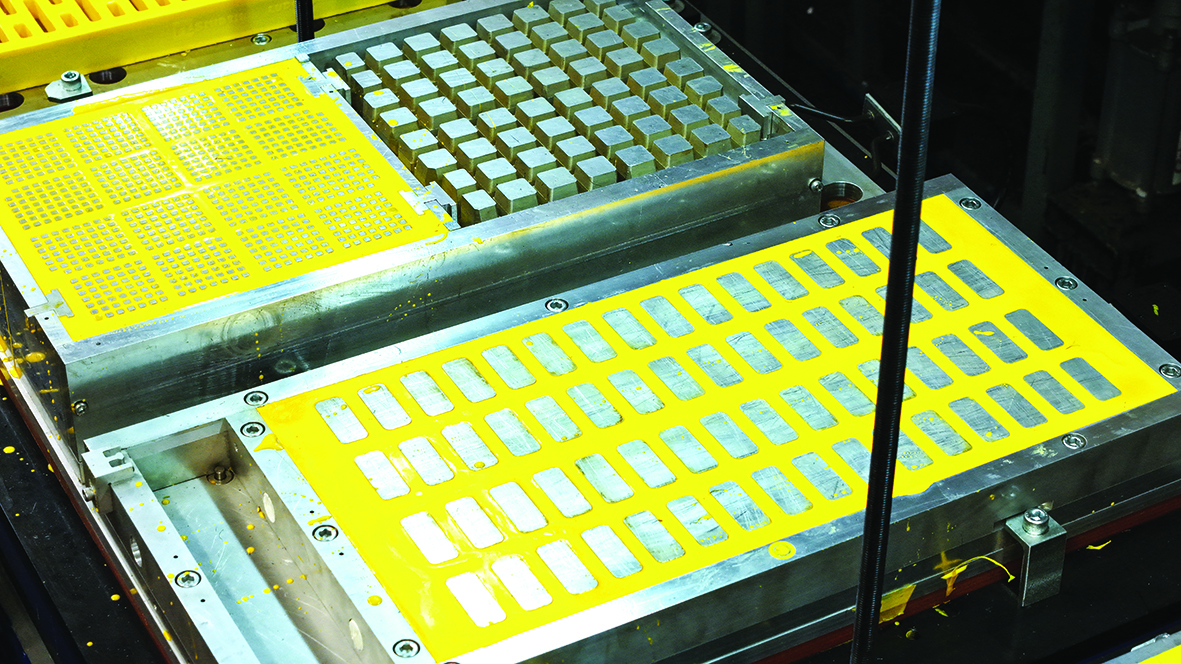
To complement this, a high capacity polyurethane machine capable of pouring up to 42 kg per minute is in operation at the facility. This system is particularly suited to applications requiring large volume pours, such as flotation spare parts and vertical mill components.
The Delmas facility already benefited from a significant upgrade in 2019, when a state-of-the-art six-axis machining centre was introduced for tooling precision, along with robotic welding systems for manufacturing screen media panel inserts and a CNC controlled spiral welding machine to produce wedge wire products. The latest round of investments builds on this foundation and brings the facility to the forefront of global polyurethane production capability.
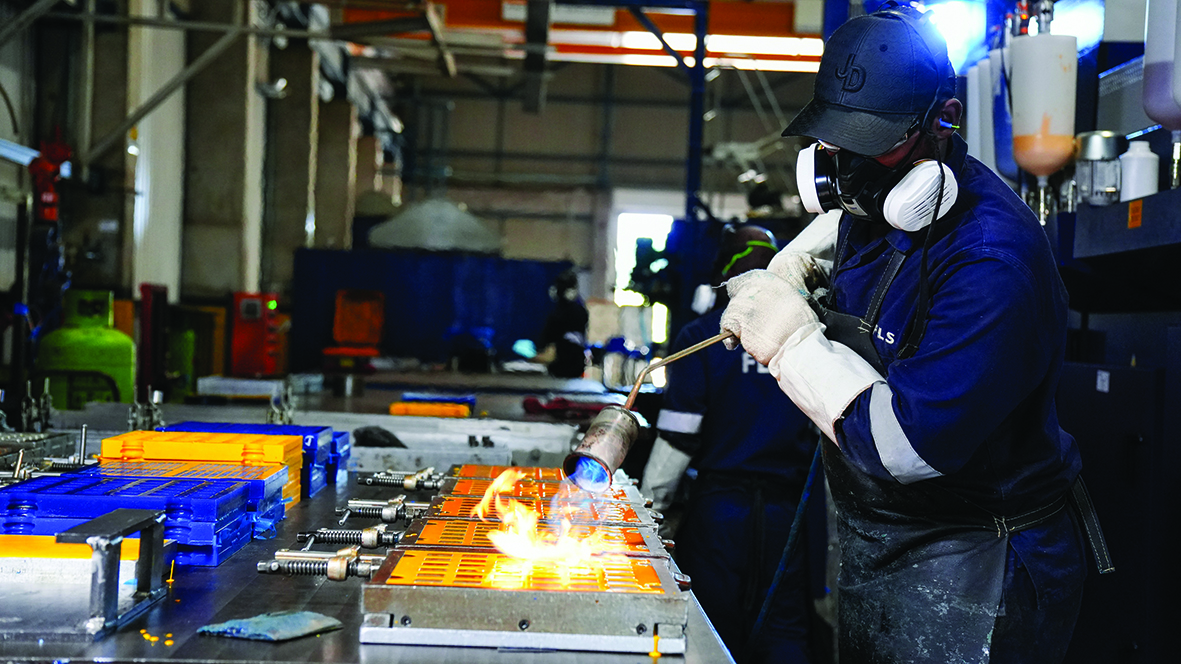
Energy efficiency was a key consideration in the new layout and equipment design. “We have incorporated smart energy saving features like individual temperature control on each casting table station,” Walker says. “This avoids the need to heat large surface areas unnecessarily and contributes to our carbon reduction goals.”
Further supporting these goals is the installation of 300 kW of solar generation capacity at the Delmas site, completed in 2024. Plans are already in place to expand this by another 500 kW in 2026, along with the integration of a battery energy storage system (BESS), enabling greater energy independence and resilience.
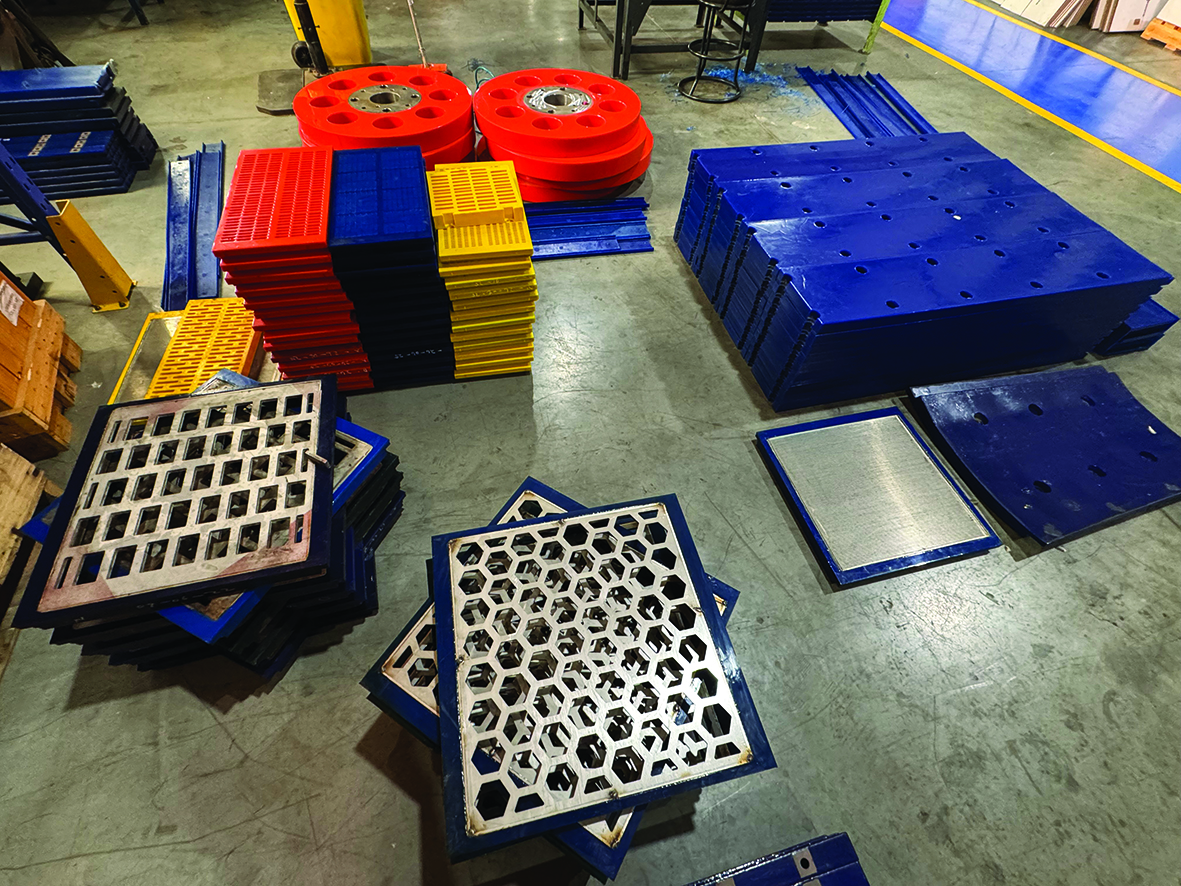
FLS’s offering from Delmas extends beyond screen media manufacturing. The facility is equipped to handle the complete fabrication of vibrating screens, from raw material processing and in-house machining to assembly and factory acceptance testing. This vertical integration allows the company to deliver customised solutions with tighter control over quality and lead times.
Shepherd emphasises that FLS operates both as an original equipment manufacturer (OEM) and a screen media specialist, supplying screen panels for all types and brands of vibrating screens, feeders and trommel screens.
“We don’t just supply products,” he says. “We work closely with our customers through our network of on-the-ground specialists to assess site conditions and select the best screening media for their specific needs.”
He notes that many older processing plants are treating materials that differ from their original design specifications. In these cases, screen efficiency can often only be improved by optimising the screen media. “This is where NexGen makes a real difference,” Shepherd says. “Combined with the correct aperture design, it allows customers to get more life and better performance from their screens.”
Unlike injection-moulded polyurethane, which can compromise the structural integrity of screen panels, FLS’s proprietary process retains superior mechanical properties, resulting in a tougher more durable product. “We have never used injection moulding because it reduces the quality of the end product,” Shepherd explains. “Our process delivers a product that stands up to the toughest operating conditions and offers lasting value.”
Walker adds that the expansion at Delmas not only supports FLS’s global operations but also contributes meaningfully to the South African economy. “Our commitment to local manufacturing is evident in the scale of our investment and the jobs we have created,” he says. “We have expanded our workforce, prioritised local recruitment and significantly grown our apprenticeship programme.”
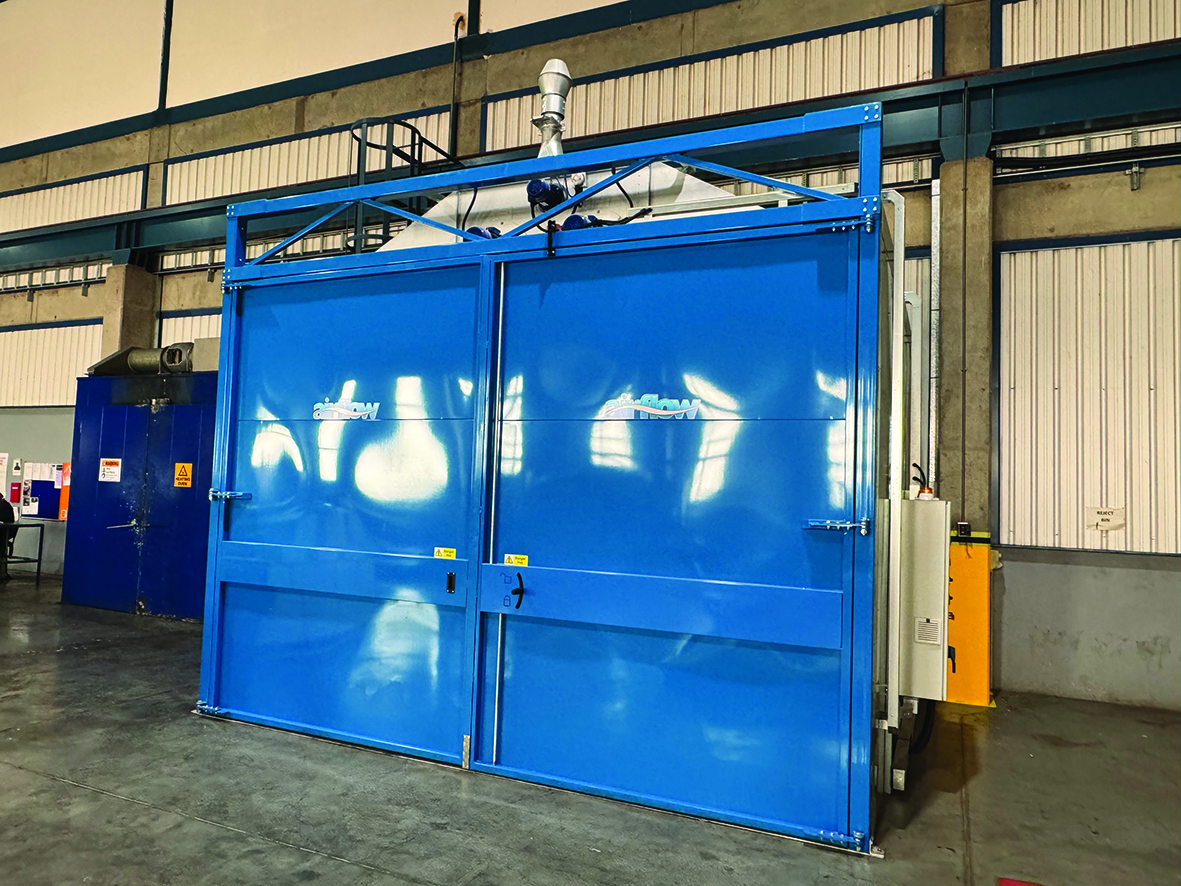
A strong focus has also been placed on developing female artisans. In 2024, six women from the local community were recruited into a three year trade apprenticeship programme, receiving training in welding, fitting and boilermaking.
“Our investment during a period of economic uncertainty underlines FLS’s long term commitment to South Africa and to our customers in the broader EMEA region,” says Walker. “We are not just building products – we are building skills, opportunities and partnerships that will power sustainable growth for years to come.”