Mines are notoriously difficult to digitize because many of the production processes are driven by environmental variables. There’s no way to know exactly how long your mine will be active or how much extractable material lies beneath the surface. That’s something that’s left up to Mother Nature.
For that reason, it’s never been about narrowing in on exact quantities; it’s about having the right technology at your fingertips to be as strategic as possible with your blasts. The way to achieve this? More data, greater accuracy.
Not only is greater accuracy a catalyst for productivity, but it also chips away at risk. When Orica started using Propeller, safety was top of mind, but the benefits of quick, easy data share soon extended beyond their initial needs.
This is the story of how blasting behemoth, Orica, used survey-grade data to defy contractor-customer norms and eliminate information silos for one of their clients—Union Bridge Quarry.
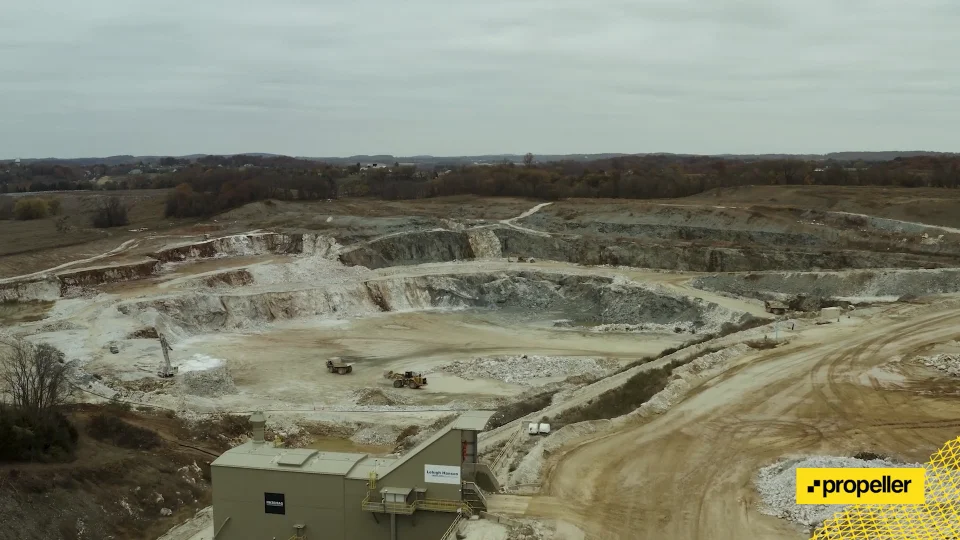
2D laser profilers stalled productivity and created unnecessary risk
Orica’s the largest provider of blasting and commercial explosive services in the world, with over 11,500 employees serving customers in 100 different countries. Trying to keep thousands of geographically-scattered employees safe isn’t easy, especially when they’re working with explosives day in and day out.
Keeping data share transparent and consistent has been Orica’s defense against accidents, and they’re constantly searching for new technology to feed, grow, and refine those data streams.
Naturally, the best way to reduce the opportunity for risk is to scale back the amount of time you spend on the active floor. But in order to capture the data they needed in order to plan blasts, they had to be out there in the thick of it.

Technicians were climbing down to the floor of the quarry to position 2D laser profilers in front of the blast face. Down there, they’d be dodging heavy equipment and stalling progress for their customer, who had to cease production each time Orica wanted to design a new blast.
This created a lose-lose situation: high-volume blasting customers lost money every time they had to pause operations and being in front of the blast face compromised Orica’s safety.
Here’s a summary of some of the problems they were encountering:
- 2D laser profilers required Orica technicians to be in the pit
- Whenever they were collecting data, their customers had to pause operations
- Heavy equipment and dangerous terrain created unnecessary risk
Orica needed to find a solution that took them out of the pit and increased accessibility to up-to-date topographical data at the same time. Their search brought them to Propeller’s PPK solution.
“Propeller PPK’s easy, and most importantly, it keeps us safe and out of the way, while still delivering the results that we expect and that our customers expect.”
Cara Rosen, Technical Service Lead at Orica
Propeller PPK helps Orica plan better blasts, while staying out of harm’s way
Propeller PPK is an end-to-end survey workflow that combines DJI’s Phantom 4 RTK drone, smart ground control points called AeroPoints, and 3D mapping software to get users the progress data they need quickly, without sacrificing accuracy.
For Orica, PPK represented the key to keeping their team safe and delivering on their promise to get the most out of every blast.

Now, they plan their flight from the Phantom 4 RTK’s controller, and step back as the drone autonomously flies their customer’s site. No more battling minimal surface area on the active floor, or trying to stay out of the way of running equipment.
After the flight, Orica uploads thousands of geotagged images to the Propeller Platform to generate an interactive 3D model of whatever site they surveyed. Within the platform, they can calculate blast volumes with 1/10ft accuracy.

Safety has always been the driving force for Orica’s technological adoption, but there have been some incredibly positive side effects that they hadn’t anticipated—the most interesting perk being how it’s helped them build stronger relationships with customers.
They’re sharing their PPK data with customers to close the communication gap that typically exists between contractors and clients. With this data, Union Bridge has greater visibility into their progress than ever before, and that visibility is saving them millions.
Lehigh Hanson’s Union Bridge site goes from yearly to monthly surveys
Nestled in the small Maryland town of Union Bridge, lies a massive quarry that’s owned and operated by Lehigh Hanson, a HeidelbergCement Group subsidiary. They’re one of Orica’s larger customers, producing close to 70,000 tons of limestone weekly, 3.5 tons annually—a massive amount of material.
Since the quarry opened, they’ve been limited to yearly surveys. Once a year, they hired a contractor to collect aerial data with a helicopter or airplane, and that’s all they had to work with for the 364 days to follow.
When you’re constantly shifting the earth and moving material from one location to another, your site changes form daily (if not hourly), and survey data is quickly rendered obsolete. Because Union Bridge had no visibility into what was going on between flyovers, costly mistakes would drag on for months before they were flagged.

“The ability to get a flight once a month, instead of once a year gets us more real-time data. What we’ve seen is occasionally walls will become out of alignment before they should be. We can correct that within the month, opposed to within the year. For us, that’s millions of dollars we’re getting back by being able to correct that.”
Greg Johnson, Engineering Project Manager at Lehigh Hanson
Orica flies their site once a month now, and relays all the survey data to the Union Bridge team. They’re now using Orica’s surveys to guide decision making for the whole quarry and examine what’s going on month to month, rather than year to year.
Orica considers Union Bridge the technological jewel for Lehigh Hanson North America because they’ve fully embraced all the opportunities for advancement that Orica’s offered, from mapping out their quarry with Propeller every single month, to drone profiling and photogrammetry.
Open data share creates “synergy” between contractor and quarry
PPK hasn’t just increased safety and productivity, it’s laid the groundwork for a long-lasting, symbiotic relationship between Orica and Lehigh Hanson. There’s a synergy that’s gained from open data share that’s brought the two teams closer together.

Orica gets the up-to-date information that they need to plan and execute blasts effectively, and Union Bridge repurposes that data to track progress and answer hard questions about their day-to-day efficiency.
Propeller’s PPK has made life easier for thousands of Orica technicians and the hundreds over at Union Bridge that were previously operating in the dark. Suddenly, the right information is in front of everyone who needs it, and both teams are experiencing heightened levels of productivity.
Orica’s technical service group is using the flyovers not only to upload to Propeller and produce 3D models that they use for blast dynamic analysis, but they’re also using technological advancement as a competitive advantage.
Here we have two very different needs, two very different agendas, served and unified by a singular source of data. Simple, 3D visual representations of where Union Bridge is at have become the bridge between contractor and quarry—the tether that keeps everyone connected.