A coal-fired generating station in Arizona required extensive repairs and upgrades. Chemical attack and the subsequent corrosion had to be tackled to prevent a repeat of a catastrophic failure experienced in 1999. The problem was remedied by repairing the effected systems and components and providing a coating to prevent further corrosion.
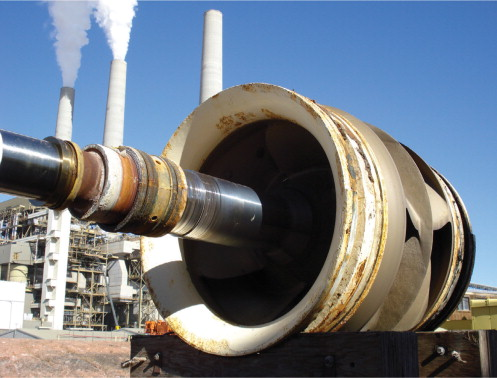
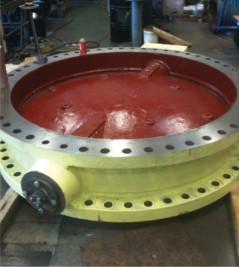
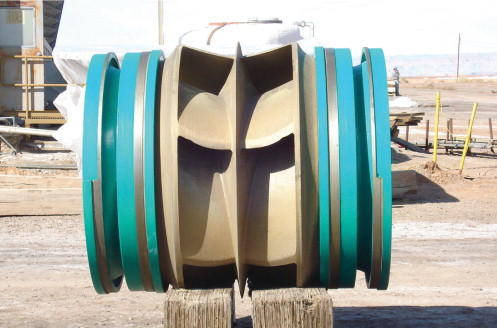
During a massive nine-week outage at the expansive power facility in Page, Arizona, Quadna serviced and repaired several critical pump systems and components. The Navajo Generating Station (NGS) is located on the Navajo Indian reservation near Page. The 2,400 megawatt station has three 800 megawatt coal-fired units which serve electric customers in Arizona, Nevada and California. The station also supplies energy to pump water through the Central Arizona Project.
The facility’s Allis Chalmers WSDD 66 × 78 in spilt case cooling tower recirculation pump, and Pratt butterfly valves provide cooling water to the Unit 2 cooling tower. The pump pulls water from the cooling basins to the top of the cooling tower to provide an ongoing evaporative cooling effect. The butterfly valve isolates the cooling tower basins from the pump and is located immediately in front of the pump’s suction.
Cooling towers offer a wide range of challenges to maintain good water chemistry. A host of chemicals are required to maintain pH and to keep algae growth to a minimum. These chemicals are not always compatible with the pumps and valves’ material of construction. During the major service, repair and overhaul, observations were made; the team was concerned that chemical attack was wrecking havoc on the giant butterfly valves and pump shaft. The team wanted to ensure the system not only received important repairs and replacements, but that the components could be better protected against aggressive chemical attack.
Quadna was asked to repair the two 66 in diameter Pratt butterfly valves, each weighing close to 12,000 pounds. The valves were connected to the split case recirculation pump, which had suffered from problematic shaft issues during the past several years. This particular pump used two shaft sleeves on each side of the impeller and had experienced extensive chemical attack at the sleeve interface. An intense and localized corrosion was present under the sleeves and at the interface caused by a corrosive effect know as crevice corrosion. In order to be an acceptable site for this type of corrosion, the crevice must be large enough to allow liquid to enter and narrow enough to maintain a stagnant zone.
The team determined that the corrosion was substantial and had to be mitigated. If left unchecked, it would potentially have led to a catastrophic failure.
According to Dana Smith, planner/scheduler for Salt River Project (SRP), the facility had a catastrophic failure, which resulted in a shaft breakage in its Unit 1A circulation pump in 1999 due to crevice corrosion.
“Last year we were able to inspect one of the new shafts installed a number of years ago,” says Smith. “We saw the same effect in the shaft sleeve to bell, sleeve o-ring area. Vic, along with our engineering department, made recommendations for weld repairs. Noting this condition in 2009, we were able to determine that this could be happening on all six in-service shafts. The Unit 2 circulation pump rebuild confirmed the corrosive attack in this area with respect to the others in-service. In 2009, it was determined that shaft replacement was the best option so a new shaft was ordered. Unfortunately, we were not able to install the shaft, because the manufacturer had threaded the end to a specific rotation; it was not what NGS had specified for the new shaft.
Quadna’s proactive response to the crevice corrosion condition was to modify the sleeve-to-sleeve sealing area to eliminate the crevice corrosion. This approach not only would prolong the life of the shaft, but also reduce and/or eliminate the need for expensive shaft replacement.”
Smith says that in 2009, SRP was also concerned with the condition of the pump impellers, the amount of wear/damage to vanes and material loss.
“These impellers have been in-service for 30-plus years,” adds Smith. “We ordered a new impeller, but unfortunately the manufacturer could not meet our need date so we had to put a bad impeller back in-service. In early 2011, we will begin the replacement of impellers on Unit one, followed by others during future outages. This was the best material option with least cost on new impellers and provided us with technical support that often is non-existent with other vendors.”
In 2008, Smith says it was time for the 66 in Pratt butterfly valve rebuild. The engineering, service and repair team had been monitoring the pump system and components for a number of years including the last several outage overhauls. Through keen observation and ongoing base metal checks and testing for progress of chemical attack, the group determined when to schedule the needed repairs, replacements and system enhancements.
In addition to the pre-determined service and repairs, which typically occur every six years for a major outage and every three for a minor one, the recommendation solutions included coating all of the surfaces where the chemical attack was prevalent to reduce future wear. The coating solution approach was approved by SRP for implementation.
Once the team agreed upon the chemical corrosion solution for the uncoated areas in the valves and shafts, work got underway. First, the shafts were machined, sleeved and seal welded.
The pump’s cast iron casing rings were coated with 3M Scotchkoat 134. The aggressive chemical attack had affected the cast iron housings and base metal, causing the base to lose its competency. The 3M Scotchkoat fuse coat now helps prevent hydrochloric acid from destroying the rings (and the valves).
The Allis Chalmers split case recirculation pump also received a new impeller, wear ring housings and related components. Quadna recommended and used a combination of coatings on the pump and valve. The team suggested and changed the impeller from a nickel aluminum bronze (Ni Al bronze) to stainless steel 316 to further ensure a long service life and more efficient operating dynamics.
The service and repair of the recirculation pump, butterfly valves and components for the Navajo Generating Station’s cooling tower system was a team effort from start to finish. Quadna, and the Navajo Generating Station team, assisted with the huge service and repair effort with the support, participation and guidance of the SRP team. Together, they made important decisions and implemented their solutions and recommendations to ensure the power plant’s system would be enhanced, well serviced and viable for several outages to come.
The evidence of Quadna’s approach to this outage, one of many it has been a part of over the years, is SRP’s continued relationship with Quadna, which has provided upgrades and solutions for these types of cooling tower applications. In addition, the coatings and other service, repair and replacement recommendations resulted in equipment which is running smoothly and efficiently since being put back into operation.
“Quadna put together the valve rebuild and the coating solution to prevent chemical attack on the valve body and internal components,” says Smith. “The technical support, proactive response to the needs of NGS and knowledge of this equipment assisted us with respect to our six-year major overhaul intervals run time, and in providing the best solutions to problems and to providing technical support specific to this industry’s type of corrosive and abrasive operations, which are inherent to coal-fired generating stations.